Voith: Reliable, flexible and efficient quality measurement and control OnQuality successfully commissioned at customers Smurfit Kappa, WEPA and Johns Manville
News General news
- Successful commissioning of quality control systems (QCS) OnQuality at various customers including the nonwovens sector
- Fast rebuild achieved within only 12 hours
- OnQuality.Scanners can be used flexibly, also rotated by 90°
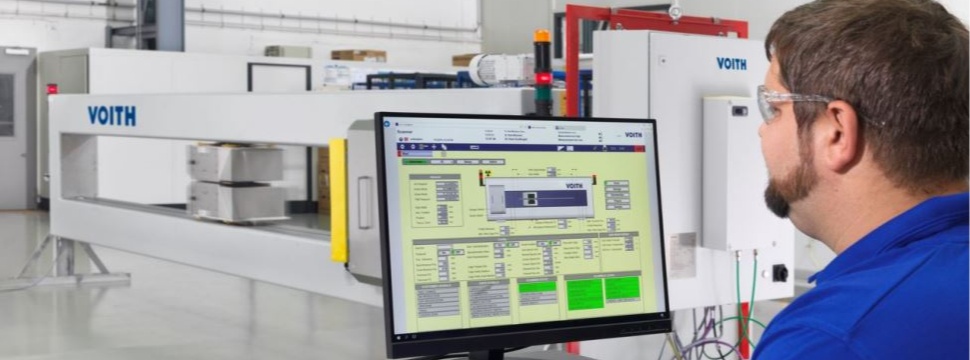
Quality control systems are an important factor in paper production to continuously optimize production and quality processes. Thanks to their compact design, flexible use and high reliability, Voith's OnQuality quality control systems (QCS) have already been used in over 750 installations worldwide on existing and new lines. The system can be used for all paper grades as well as for nonwovens.
Positive customer feedback – from Smurfit Kappa, WEPA and Johns Manville among others – confirms Voith's leading position.
"The smart solution OnQuality from our Papermaking 4.0 automation and digitalization portfolio stabilizes and optimizes the production process, increases productivity and at the same time reduces operating and maintenance costs", said Mahmut Altunkaya, Lead Engineer QCS at Voith Paper.
The high flexibility of the system is particularly evident in the project with customer WEPA. Here, the solution was installed at TM 1 in Mainz, Germany.
"We decided to replace our existing QCS with Voith OnQuality because of the short rebuild and commissioning time of only 12 hours, as well as the seamless and individual integration into our existing process control system", Jürgen Birk, Mill Manager Mainz at WEPA.
Especially for tissue paper manufacturers, Voith offers scanner models that are equipped with covers and additional cleaning nozzles for the measuring carriage. They facilitate cleaning and maintenance work and improve the accuracy of the measurements.
Due to the high level of satisfaction with the new quality control system, the tissue paper manufacturer decided to take another step on the road to digitalization with Voith. As part of OnQuality 4.0, the Voith Cloud platform will in the future collect and store all relevant production and quality data from the TM 1, enabling WEPA to perform in-depth analyses via personalized dashboards. With just a few clicks, profile charts, color maps, maintenance cockpits, trends and reports can be intuitively created and viewed on mobile devices. In addition, the use of a virtual sensor will complement the physical measurements and thus quickly and directly reveal deviations in the critical target quality in a profitable manner, which can otherwise only be measured in the laboratory on a sample basis.
Individual solutions for optimum quality measurement and control
Smurfit Kappa Herzberg mill also commissioned Voith to install an OnQuality quality control system at KM 1 at the Herzberg am Harz site, Germany.
"Due to the very compact and flexible design, only Voith was able to fulfill a challenging installation position with a necessary 90° pivoting of the scanner. Now we can determine exact measured values even in this difficult location", said Danny Polske, Maintenance Manager at Smurfit Kappa Herzberg mill.
The OnQuality quality control system is used here as a stand-alone system with a direct connection to the existing process control system.
Another order from Johns Manville shows that the quality control system is also suitable for use in the nonwovens sector. At VLM 15 in Steinach, Germany, the OnQuality Nonwoven Caliper Sensor is now used in addition to a special filter for measuring binder content. The Voith caliper sensor for nonwovens is specially designed for nonwoven applications. This effectively prevents marking or damage to the web.
"Thanks to the Voith QCS system, we can better monitor our manufacturing process and intervene in time if necessary. This allows us to optimize our product quality and increase efficiency", said Thilo Behringer-Stephan, Electrical Engineering at Johns Manville.