Monitoring losses with the digitalization solution OnView.MassBalance for more sustainability and transparency in stock preparation
News General news
- OnView.MassBalance visualizes losses in stock preparation and thus enables operators to take appropriate countermeasures easily and at an early stage
- Thanks to the digital solution, significantly more resource-efficient paper production is possible
- Successful customer installations demonstrate a two percent improvement in total yield
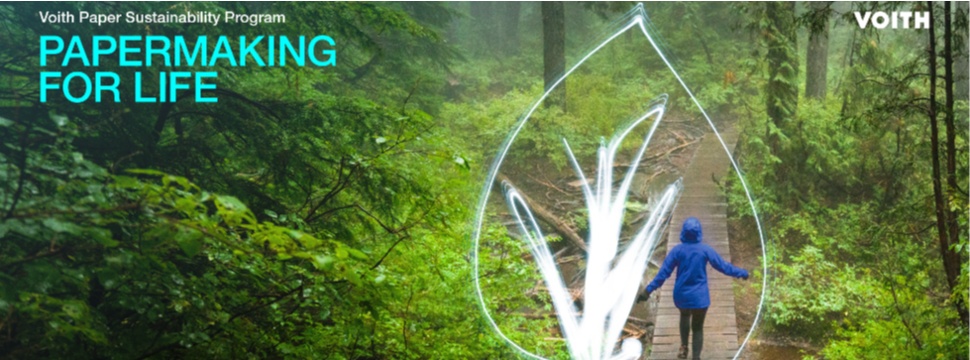
The recycling process in paper production is complex. Fluctuations in fiber quality and the degree of contamination of the recovered paper bales have a direct influence on production output. At the same time, resource efficiency is more important today than ever before. However, with the current state of the art, it is hardly possible to determine the specific causes of losses and optimize them directly. Yield is usually only measured on a weekly or monthly basis - by the time paper manufacturers receive the information, the losses have already occurred. Furthermore, it is very difficult to estimate whether losses in individual stock preparation areas have increased or decreased compared to the last analysis. To address these issues, the leading full-line supplier Voith has developed OnView.MassBalance.
The innovative digital tool displays losses in stock preparation in real time to further increase the sustainability and efficiency of paper production. At a glance, the operator can locate the specific areas with optimization potential on the screen. For this purpose, a Sankey diagram maps each feed, accepts and rejects at each process step. As soon as a critical value is reached, OnView.MassBalance reports this to avoid high losses. In this way, standardized processes can be established that can be quickly and easily performed by operators across different shifts. Suitable countermeasures can be, for example, checking the pressure drop or the feed consistency of the last screening stage.
As there is less rejects to dispose of and at the same time more paper can be produced with the same amount of raw materials, the solution pays for itself in less than a year. Flavio Granito explains:
"The solution is already being used very successfully, for example in an OCC mill in France with an annual capacity of 250,000 tons. After the optimization phase, 600 tons of rejects, including raw material, could be saved per month. This corresponds to a two percent improvement in yield. OnView.MassBalance is another example of how digitalization can strengthen more sustainable and cost-efficient papermaking. As part of our major sustainability program Papermaking for Life, we have set the goal of optimizing recycling processes and minimizing fiber losses. We aim to achieve a 90 percent recycling rate by 2030."
Installation and operation support
To calculate the mass balance in stock preparation, the innovative tool uses the signals from the sensors installed in the stock preparation plant. Voith experts identify the sensors required for this and develop a suitable concept together with the customer. Voith also separately offers the OnPerformanceLab (OPL) service. Based on bundled know-how, the OPL provides pragmatic support in analyzing losses, defining and implementing new countermeasures, and preparing monthly reports in close coordination with the respective paper technologists.
Sustainability program Papermaking for Life
Optimal production and resource savings with the help of the Papermaking 4.0 digitalization and automation portfolio are key topics of Voith’s Papermaking for Life sustainability program. As part of the innovation and development offensive, Voith Paper presents versatile technologies and initiatives that lead to more efficient and sustainable processes in paper production. The focus is on water, energy and fiber savings as well as digitalization, innovations and partnerships as levers for more sustainable production.