Combined competencies of Voith and Meri lead to significant water savings in paper production
News General news
- Building on many years of experience, in-depth know-how and leading solutions, Voith and Meri offer an optimally aligned portfolio
- Tailored process solutions in the areas of water, sludge and residuals have improved the profitability and sustainability of many customers worldwide
- AquaLine water management system already in widespread use
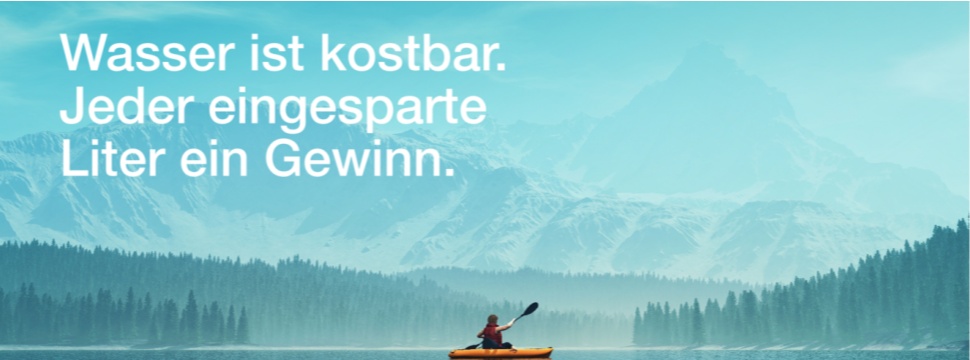
The global interest of papermakers in water-saving solutions has steadily increased, with the effective use of water as a resource is an essential lever for sustainable paper production. To support papermakers in securing their future competitiveness, Voith and its subsidiary Meri have been developing tailored new innovations in the areas of water, sludge and residual materials for more than 25 years. Mutual understanding of the product portfolio, very close coordination in every project phase and many successfully completed projects characterize the partnership of the companies.
"Over the years, we have developed unique process know-how. Combined with our highly efficient technologies, this make Voith a strong full-line partner for manufacturers of all paper grades who want to take their operations to the next level of performance in the area of sustainability", Axel Gommel, Global Product Manager Fiber Systems at Voith Paper.
In successful cooperation, Voith and Meri experts offer fresh water treatment and conditioning as well as internal cleaning of process water streams. In addition to process and disposal machines, their extended portfolio also consist of wastewater treatment including primary, secondary and tertiary treatment via chemical or physical stages. These are combined with anaerobic and aerobic biological processes and sludge treatment. Customers also benefit significantly from Voith and Meri's water and wastewater balances. Furthermore, Meri offers optimized solutions for the rejects recovery process stages, such as transport, handling and conditioning, and waste-to-energy processes.
In addition to the optimized product portfolio and close cooperation, global presence is also a key success factor.
"Thanks to the combined synergies of Voith and Meri, we are very well positioned and networked internationally", says Henning Laubrock, Head of Sales & Technology at Meri.
Voith now boasts more than 110 OCC stock preparations with a total production capacity of more than 40 million tons per year over the past 20 years. Meri has realized more than 5,000 installations and supplied more than 300 subsystems. With the opening of another site in Kunshan, China, Meri strengthened its local footprint in the APAC region, supplying efficient water, sludge and reject (WSR) and wastewater systems to Chinese and other Asian customers, among others.
According to Laubrock, a major milestone of Voith and Meri was the joint development of the sustainable water management system AquaLine. Following the official launch of the system in 2021, the AquaLine, AquaLine Flex and AquaLine Zero system variants are already in use at several well-known manufacturers of packaging paper. Among others, the North American paper manufacturer Green Bay Packaging uses the AquaLine Flex system variant at its PM 4 in Wisconsin. Equipped with a "biological kidney," the process water can be treated and part of the purified process water fed back into the production process. The amount of wastewater is thus reduced to up to 3.5 liters per kg of paper produced. Compared to similar production plants, Green Bay Packaging with an annual production volume of 621,422 tons and a design speed of 1,200 m/min saves fresh water amounting to 2,271 m3 per day. Comparable process values and savings can also be found in the plant of Turkish paper manufacturer Kipaş Kağıt, which started up in mid-2022. In addition, Kipaş Kağıt produces around 90 MW of electrical energy from biogas produced in Meri's anaerobic wastewater treatment plant and fed directly into the public grid.
"The AquaLine Flex system variant has now become state of the art in the production of packaging papers. In addition, under certain conditions it is possible to operate plants with the closed, technologically very complex water circulation system AquaLine Zero, in which the process wastewater is reduced to zero liters", says Axel Gommel, Global Product Manager Fiber Systems at Voith Paper.
In the future, Voith will continue to develop the individual concept variants so that closed water circuits can increasingly be used throughout the paper industry. In addition, as part of Voith’s Papermaking for Life sustainability program, the company is also working on new, disruptive solutions to significantly reduce fresh water consumption.