Valmet to supply an extensive recycled fiber line and paper machine grade conversion rebuild to Model Paper Eilenburg in Germany
News General news
Valmet will supply an extensive paper machine grade conversion rebuild with an automation package to Model Paper Eilenburg in Germany. In the project, the paper machine, which currently produces newsprint grades, will be rebuilt to produce lightweight, recycled containerboard grades. The start-up is scheduled for the beginning of 2024.
The order is included in Valmet's orders received of the fourth quarter 2021. The value of the order will not be disclosed. The total value of an order of this type and delivery scope is typically around EUR 90–100 million.
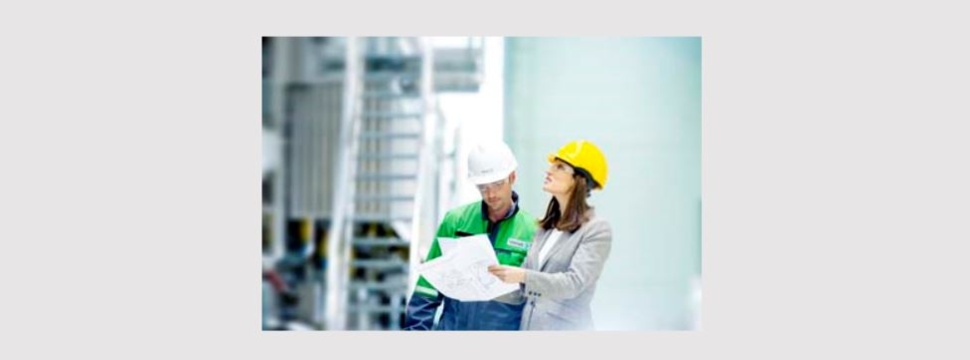
“The converted machine will focus on the production of lighter grammages and will therefore meet the customers’ demands in the future. The containerboard production volume of Model Group will be more than doubled after the successful conversion. We trust Valmet’s technology to fulfil our goals,” says Jürgen Lemke, COO, Paper Unit of Model Group.
“This is again a very interesting project for Valmet in Europe. The technology and references we presented to Model Group were well-suited. The production line has many technical highlights: a new linear double shoe press to improve machine runnability and end-product quality, and the extremely high-capacity winder and Valmet DNA Automation system for the whole machine line will ensure that the delivery meets Model’s goals,” says Tobias Hain, Senior Sales Manager at Valmet.
Technical information about the delivery
Valmet’s grade conversion delivery will include a rebuild of the DIP (deinked pulp) line and OCC (Old Corrugated Container) line, updates to stock preparation, and a rebuild of the board machine.
The OCC line will be featured with upgrades to HC cleaning, coarse screening, and LC cleaning to increase the capacity and the handling of brown fiber. Fiber fractionation and long fiber fine screening maximize the efficient stickies removal. Underneath the machine, a new broke collection minimizes the consistency variations, and machine screening ensures the final fiber quality.
The delivery for the board machine rebuild will include a shoe and blade technology upgrade in the forming section and a new OptiPress Linear press section. The drying section will be updated into OptiRun Single. The delivery will also include an OptiAir Hood high-humidity hood, OptiAir Recovery heat recovery system, and other runnability, dryer and air system equipment to improve the drying efficiency and runnability and to enhance draw control. After the drying section, a new OptiSizer Film sizer with a supply system, an OptiReel Linear reel, and a very high-capacity OptiWin Pro winder will be included. The delivery will also include a paper machine clothing package as well as maintenance master data to ensure an efficient and disturbance-free production.
The delivery will be complemented with the latest generation Valmet DNA Automation System, including built-in process control, machine control, sectional drive control, quality control, and condition monitoring. Additionally, Valmet IQ Quality Control System (QCS), Valmet Paper Lab, IQ Web Inspection System, IQ Dilution Profiler, IQ Steam Profiler, and IQ Moisturizer will be included in the delivery. Valmet Wet End Analyzer and Valmet Retention Measurement will provide valuable information on the process.
The board machine with a 10,050-mm-wide fabric will produce fluting and testliner grades with a basis weight range of 70 –120 g/m2. The design speed of the new parts will be 2,000 m/min with a daily capacity of approximately 2,000 tonnes.