Thimm invests almost EUR five million in a further processing machine at the Northeim site
News General news
Packaging and display manufacturer Thimm is investing in its Northeim site in southern Lower Saxony and is commissioning a new inline system for the further processing of corrugated cardboard. Thimm is therefore continuing to align the plant to the increasing requirements in the consumer goods and e-commerce sectors.
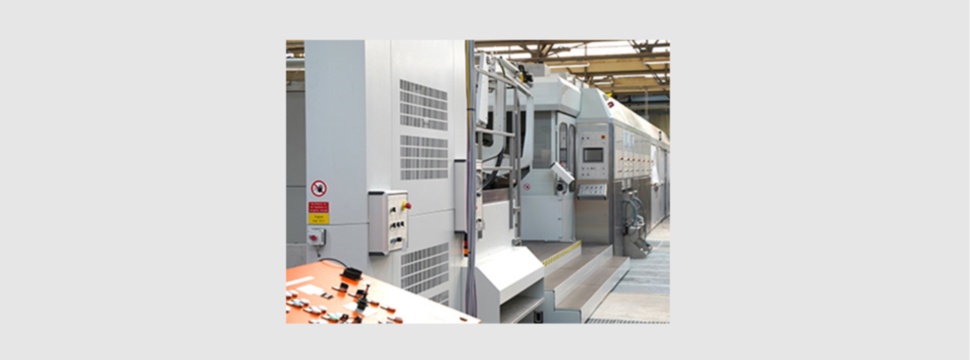
With the commissioning of the BGM Case Line CL11/25 inline system from the two German machine manufacturers Bahmüller and Göpfert Thimm Group is setting new quality standards in the further processing of corrugated cardboard. To achieve this, the company has invested almost EUR five million in the new high-performance system and in the necessary peripheral works in the plant. The fully servo-driven BGM Case Line has an operating width of 2.50 metres and expands production capacity of high-quality printed and precisely processed folding boxes for everyday consumer goods and shipping packaging for e-commerce. With individually driven axes and the associated high register accuracy, laser-engraved anilox rolls and a camera-supported blade system, the system ensures an exact and high-quality post-print printing result. Other factors such as a quick-change rotary die-cutting unit, a precise slotting unit with direct drive and a powerful folding station also contribute to an optimum end result and increased productivity.
During processing, the corrugated cardboard sheets are transported in a vacuum with precision through the machine. Incorrectly glued individual sheets can be detected using an integrated camera and ejected directly, even at maximum production speed. Finally, a high-performance palletising robot prepares the produced goods for pallet-free further transportation. “This investment is an important step in the expansion of our packaging plants and places the Northeim site in an excellent position enabling us to fully meet our customers’ high future requirements in terms of quality and capacity of our production,” emphasises Michael Weber, Director Corporate Strategy + Marketing at Thimm Group.
The integration of the large system into the existing hall plan posed a particular challenge. “However, working together with the manufacturers, we were able to find a customised solution, despite limited space, for the optimum integration of the long machine into our plant without having to compromise on performance,” reports Weber. The new system is now mirrored to the existing inline machine and has therefore created a new production centre in the plant. To this end, since 2019, preparatory measures including the relocation and modernisation of existing plants, have already been implemented at a cost of EUR one million. In addition, two rotary die-cutting units were mirrored next to each other in the factory which have now also created another production centre. “This parallel positioning within the two production centres has yielded valuable synergy effects for us, as the employees deployed can work efficiently together as a team on both machines. This facilitates personnel planning, for example, and also enables flexible job rotation,” explains Weber. And furthermore, “with this investment, we are consistently aligning the plant to the current and future needs of the consumer goods and e-commerce sectors.”