Stora Enso's biogas partnership with Gasum turns waste into green energy
News General news
The production of Multicopy paper is about to contribute to the biofuel production in Sweden. The energy company Gasum and Stora Enso will together turn waste into renewable green energy.
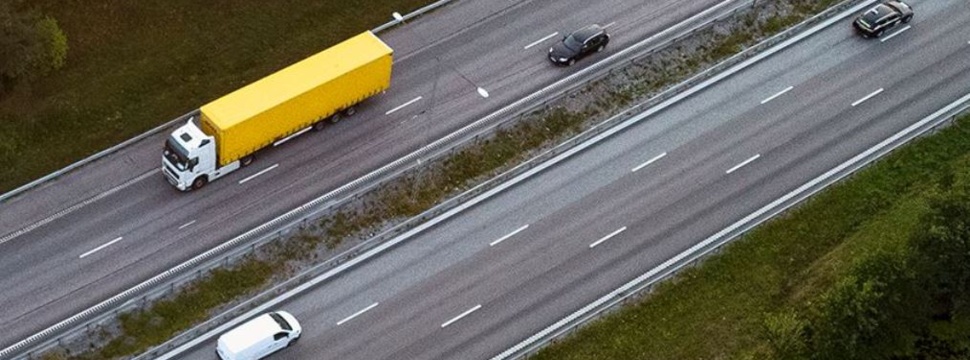
Wastewater can be a challenge for mills. Vast volumes of process water containing organic residues need to be treated. At the Stora Enso’s Nymölla Mill, the water treatment facility is the size of ten football fields, and each holding basin is seven metres deep.
“Nymölla Mill has long been a leading light in sustainability,” says Jonathan Bakewell, VP, Office Papers, Stora Enso Paper Division. “Even though today the paper production process is essentially carbon-neutral, they always want to do more.”
“We’ve been looking into biogas for many years,” confirms Michael Lindemann, Mill Director at Nymölla. “When we initially determined biogas could be made from our process water, we wanted to use it to power the mill.”
As renewable energy rose on the global agenda, the idea evolved into selling biogas. Given the challenges that remained, teaming up with a partner who really knows biogas was the best way forward.
“I have talked with Stora Enso in different roles throughout my career in Swedish biogas,” says Erik Woode, Director, Biogas Business Development at Gasum. “When Gasum came into the picture on this project, it really was a game changer.”
Gasum not only brings technical know-how in producing biogas, but also has a distribution network. These factors help to make the biogas partnership a powerful combination from which Stora Enso, Gasum and the environment all benefit.
Creating value from waste
Looping the mill’s process water through the biogas reactors breaks down the organic content to produce methane. This process reduces the organic content up to 60 per cent after just five hours in the reactors, leaving far less to be treated in the wastewater facility.
This project is a wonderful opportunity for Gasum to demonstrate how biogas is a viable renewable fuel made from what would otherwise be burdensome waste for mills.
“The key here is that today we can liquify the biogas,” explains Woode. “Historically it was quite expensive to do that, but technology has advanced to the point where we can do it economically.”
Liquified biogas (LBG) is comparable in energy-density to diesel fuel, making it ideal for the heavy transportation sector, a major source of carbon emissions. LBG emissions are 90 per cent less than diesel, and LBG produces far fewer particulates, further minimising impact on air quality.
Replacing liquid natural gas (LNG) with LBG is the immediate goal. “LBG is what we call a drop-in fuel,” explains Woode. “It is 1-to-1 with LNG, and we are hurrying now to fill our stations with LBG because that is what our customers want.”
The LBG from Nymölla will improve the overall balance of renewable energy in Sweden considerably, accounting for a 5 per cent increase in biogas production. That’s enough to power the equivalent of 13 000 cars a year.
The excitement builds with a twist
Even with the best plans, a global pandemic is tough to mitigate. Travel restrictions and quarantines kept works from coming to the site. “We were in a difficult situation if there ever was one,” says Lindemann. “For our part, the mill is ready to go, and that was fortunate with our hot summer.”
The heat nearly killed the microbes in the water treatment facility. Luckily, the heat exchange system for the flow to the Gasum facility was already in place, so it was used to cool the effluent and save the microbes.
Final assembly of the LBG plant should be completed during springtime this year. The mill will start pumping water shortly thereafter, followed by a ramp up period as Gasum tunes operations for full capacity.
“Something that I really appreciate is that Stora Enso allowed us to build our plant right at the mill,” notes Woode. “One could say that is a complicating factor in the project, but the results have been well worth it.”
Many people are eagerly waiting to see those results. “I’m also very excited to see the project come to completion,” says Bakewell. “Not only does it make our mill more efficient, but Multicopy paper, our star product out of Nymölla, gets a wonderful new chapter as a biogas generator in its sustainability story.”