Carl Macher - the next chapter of a successful partnership - Modernization of a Goebel U20 Roller with a fully automatic slitting system from DIENES
News General news
The company
Since its foundation in 1821, the core board factory Carl Macher has always relied on know-how. Through constant development and the right selection of their suppliers, Macher has succeeded in being the most efficient core board plant in Europe. In the meantime, the factory in Brunnenthal near to Hof produces 300.000 tons of high-quality core board annually. Carl Macher has been a member of the Kunert Group since 2008.
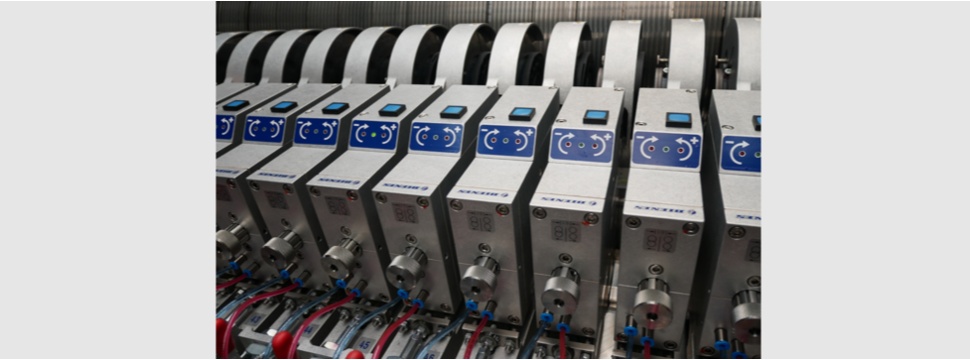
The challenge
Carl Macher’s main production line is in operation 24/7. One requirement of the modernization was to keep machine downtime as short as possible. The minimum cutting widths are 60 mm with 61 cuts. The challenge: narrow cutting widths, a little free installation space, many cuts and a short integration time. The time frame for the conversion was 48 hours.
The solution
The successful modernization of a Goebel Roller U16 in 2020, together with an excellent economic assessment, as well as a positive response from the operating personnel, built the basis for Carl Macher’s most recent investment decision in a new DIENES slitting system. DIENES is considered as a pioneer in the comprehensive modernization of existing slitting systems and has already modernized more than 1.400 slitting lines during its 110 years of history. A detailed on-site consultation, the following conceptual design, as well as the experts’ assessment convinced Carl Macher to carry out a large-scale project once again together with DIENES. The PSGs DF shear cut knife holders with Senso Control, which were already in operation, were a convincing solution in the existing plant due to the easily reproducible knife settings, the reliable cutting forces and the long service lifetimes. The knife holders are also equipped with the DIENES Quick Clamp function. Quick Clamp enables a tool-free knife holder removal from the slitting system, e.g. during knife change. The line to be modernized cuts also core paper at a production speed of 2,000 m/min. Also for this slitting line, Carl Macher decided to use the already approved knife holder PSGs DF with Senso Control and Quick Clamp. The positioning of the shear cut knife holders is achieved with the DIENES SIMU-FLASH, the proven solution for fully automatic simultaneous positioning. With SIMU-Flash, the top knives are positioned within a very short time. Customer recipes for positioning the knife holders can be stored, and when selected by the operating personnel, the top knife holders are moved directly to the stored position – with a maximum precision. The rapid movement of the knife holders into the parking area for inserting the web material minimizes the risk of injury to the machine operator, as ideal working conditions are achieved. After that, the production can be started in the shortest possible time. The positioning of the bottom multiple knife blocks is also fully automatic. Modul IV positioning technology is going to be used here, i.e. sequential positioning. This ensures minimum positioning times and also takes machine availability to a new level.
The implementation
The slitting system is built completely ready to install at DIENES production area to ensure the quickest and most uncomplicated implementation possible at Carl Macher. After running some successful tests, the slitting unit leaves the production site. This will be followed by an intensive on-site assignment from the DIENES service team to install and put the system into operation within the scheduled 48-hour period of time. The customer Carl Macher is looking forward to the installation of the new slitting unit. Thanks to the existing plant, the machine operators are already familiar with the handling of the DIENES tools.
The sensor for detecting the knife circumference and the resulting reproducible overlap depth, especially for reground knives with different diameters, contributes to consistent cutting quality and a reduction in setup costs. Individual operating failures are also eliminated and a higher level of safety is provided.
The outlook
The renewed, trustworthy collaboration shows that a relation based on partnership makes the following difference: a large project with special requirements calls for team spirit, know-how and experience. With the appropriate knife holders, the slitting system ensures not only a significant increase in productivity, but also optimized operating safety and ideal service and spare parts availability.
Without any modification to the machine set-up, the Goebel Roller U20 is going to be upgraded with the automatic DIENES knife adjustment system. The fast positioning of the system according to stored recipes, the fast movement of the knives into the parking position and back for the safe insertion of the web material and the high operating safety due to the automation contribute to maximum economic efficiency.