Schumacher Packaging drives digitalisation forward in a further step towards environmentally friendly production
News General news
Federal Ministry for Environment funds resource-efficient production technologies from the packaging specialist operational throughout Europe
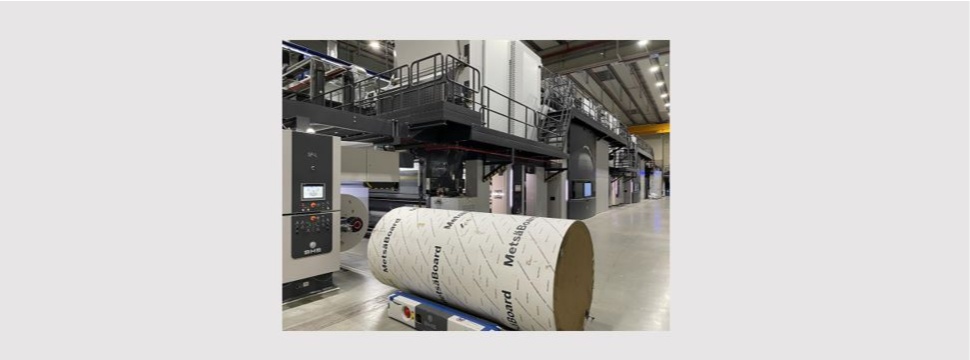
The Schumacher Packaging Group, one of the largest manufacturers of corrugated and solid board in operation across Europe, makes huge strides forward in the digitalisation of its production. For the resource-efficient "iPrep" transportation and unwrapping system at the Greven production facility –the only one of its kind in the world currently – the company was awarded a € 480,000 grant from the environmental innovation programme run by the Federal Ministry for the Environment. Yesterday, Parliamentarian State Secretary Christian Kühn presented the company with a grant certificate online. By 2025, Schumacher Packaging sets out to invest € 700 million into environmentally friendly production.
"By using a resource-efficient, automated transportation and unwrapping system at the Greven site, Schumacher Packaging is sending a clear signal about environmental protection to the packaging sector and beyond. iPrep reduces waste and, most importantly of all, significantly lowers the CO2 emissions involved in the production of paper packaging. We want to see and fund more projects like this one in the packaging industry," explains Parliamentarian State Secretary Christian Kühn at the virtual meeting.
Björn Schumacher, CEO of the Schumacher Packaging Group, highlights that "the key to a more sustainable packaging industry lies in an environmentally friendly production method. That's why we are investing in future technologies that use fewer resources in a bid to reach our target of carbon neutral production by 2035 at the latest. iPrep represents another step on our path to carbon neutrality and we are of course delighted that our commitment to the environment is receiving not only recognition but also financial support from the government." Schumacher Packaging is the world's first corrugated board manufacturer to utilise the iPrep prototypes and to further develop these in partnership with BHS Intralogistics.
The environmental innovation programme is a prestigious funding programme supporting extraordinary projects that advance the state of the art within an industry and demonstrate to other companies within the industry and beyond how innovations can help to relieve the burden on our environment.
Protecting the planet with digital technologies: iPrep as a showcase project
As an innovator and pioneer of the industry, Schumacher Packaging sets about highlighting new ways to make production more sustainable: "Using the iPrep automated transportation and unwrapping system, we can prevent around 548 tonnes of corrugated board raw paper waste at our Greven production facility, which indirectly prevents approx. 274 tonnes of CO2 emissions each year. These are impressive numbers, which can be achieved in the industry through this kind of digitalisation project," explains Björn Schumacher. He and his brother Hendrik are the third generation of Schumachers to run the family business.
At present, the paper rolls required in the plant are transported by forklift trucks and gripping clamps or low profile pallet trucks. This invariably causes damage to the outermost paper webs, which then need to be removed. Until now, this removal process has been completed manually with on average eight layers of undamaged paper being removed from the roll. With iPrep, the paper rolls are now carried by a driverless transport system to an unwrapping station, where they are unwrapped in a fully automated process. This involves a robot targeting and cutting off the first layer and forwarding the paper roll to an inspection unit. Here, LED and camera technology checks the paper web for signs of damage and initiates other cuts as necessary until the paper is completely flawless. Then, the paper roll is delivered to the corrugator machine by the driverless transport system, again in a fully automated process.
Greven site: The next generation of multi-mega-plant
iPrep is just one example of how this family business from Franconia is reacting quickly and flexibly to ever-changing market conditions. Since the summer of last year, Schumacher Packaging has been expanding the corrugated board plant in Greven into a next-generation multi-mega-plant. This expansion is the packaging specialists' response to the growing demand for corrugated board packaging witnessed in recent months, which is itself driven by the e-commerce sector. As well as extending the production floor by more than 20,000 m2, the expansion also incorporates two new corrugator machines, arriving this year. The second corrugator machine with a working width of 2500 mm is scheduled to begin operations in the third quarter of 2022. This means Greven will soon become one of the world's largest multi-mega-plants in the corrugated board sector. The expansion of the Greven facility forms part of Schumacher Packaging's investment programme, which will see the long-established company invest a total of around € 700 million by 2025 to make production sustainable and fit for the future.