Paper manufacturers increase energy efficiency through customized audits and process analysis from Voith
News General news
- Energy audits performed by Voith Paper have achieved significant energy savings in areas such steam and condensate, air handling and vacuum systems
- Papermakers can choose from a variety of energy audits, including desktop audits, on-site overview audits and detailed on-site audits
- Customers are reporting a 10 to 20 percent savings on their total energy costs
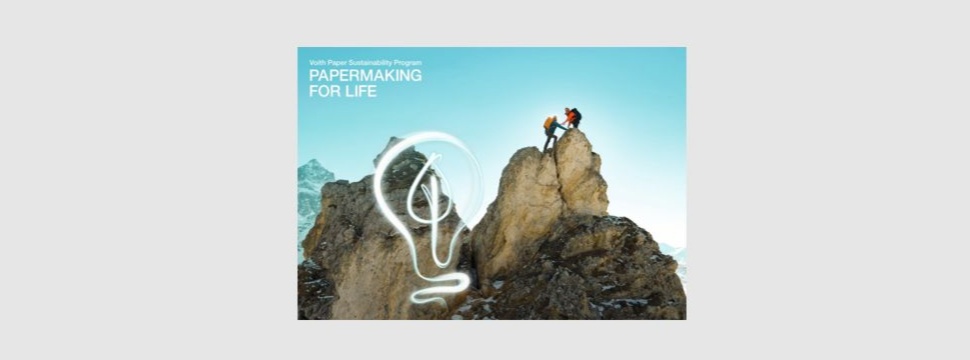
Source:
Company news
Voith Paper is helping paper manufacturers significantly increase their energy efficiency. Using customized auditing and process analysis methods, the leading full-line supplier offers innovative solutions to improve processes and increase efficiency. This allows paper manufacturers to understand the big picture of their energy consumption and find clear ways to reduce it.
Voith offers a range of services, including desktop audits, on-site overview audits and detailed on-site audits:
- Desktop audits use customer information such as equipment data and trends to provide an effective overview of energy consumption and identify ways to reduce it. The paper manufacturer receives a report with analysis, industry benchmarking, best available technologies and possible optimization projects. For example, with a successful energy audit for an Asian paper mill, Voith experts identified 34 projects that saved 20 percent in energy costs and reduced the carbon footprint by 35.7 percent.
- The on-site overview audit is designed to provide a comprehensive overview of energy consumption and a detailed analysis. This service solution includes, for example, collecting details from on-site systems, reviewing documents and assessing leakages and bottlenecks. A successful overview audit in Germany resulted in a reduction of more than 30 percent in gas consumption and savings of almost 18 percent in electrical energy. To achieve this, 28 individual projects were successfully implemented.
- A detailed on-site audit includes the collection of details from specific systems such as vacuum, steam, condensate and air treatment. With the help of special on-site measurement tools, a realistic operating scenario and a detailed study of the specific system are created. The report includes a calculation design as well as innovative ideas for process improvement and increased energy efficiency. Voith also offers support in the implementation of the projects. For example, thanks to a detailed audit at a paper mill, potential improvements in the vacuum system were identified. By making simple adjustments and without capital expenditure, energy savings of 21 percent were subsequently achieved.
Company profile: Voith Paper GmbH & Co KG, Germany, Heidenheim an der Brenz