New Valmet Retention Measurement provides more stable wet end operation from day one
News General news
Valmet introduces the latest generation of the Valmet Retention Measurement for continuous measurement of total and true ash consistencies at the wet end.
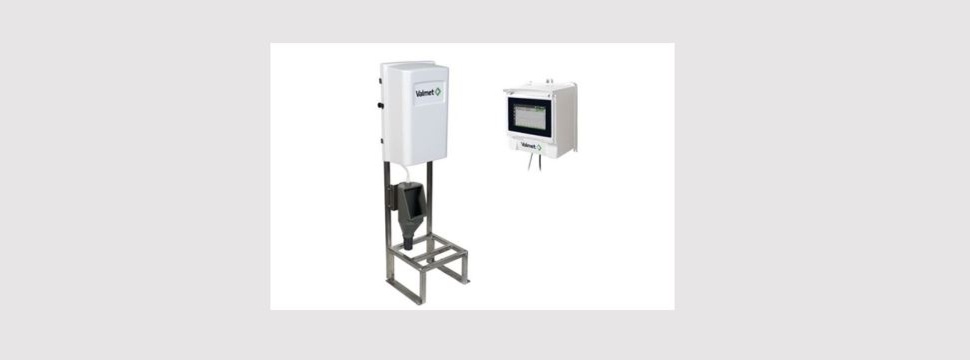
Capable of dealing with various pulps and fillers in the headbox and white-water, the Valmet Retention Measurement offers a solid base for fully automatic retention aid control to vastly improve runnability, efficiency and product quality. Pre-calibration models for various pulp types make it possible to secure valid measurement results from day one with the ability of storing up to 8 different models for smooth grade changes.
“Our challenging target was to raise the Valmet Retention Measurement, which is already recognized as the industry standard, to the next performance level. Now with superior accuracy, availability, and state-of-the-art user interface of the new generation measurement, I am confident that we have achieved that target,” says product manager Timo Rantala.
Secured lifecycle
The redesigned optics and electronics are also available for existing users with upgrades to extend the useful lifecycle of earlier generation Valmet Retention Measurement sensors.
This includes easier commissioning and operation with the Valmet Bridge user interface, a 7’’ touch screen control platform designed for use with Valmet process sensors. The sensor features comprehensive diagnostics, data storage capabilities and variety of the communication protocols with Valmet Industrial Internet capabilities to enhance performance as well as access to local or remote support.
Stabilized wet end
Control packages for the wet end that fully utilize Valmet Retention Measurement capabilities include the Valmet Stand-Alone Retention Control (Valmet RET) as well as integrated applications for Valmet DNA process control and Valmet IQ quality control systems.
Stabilized wet end operation is achieved with Valmet’s well proven white-water consistency and breaktime headbox ash control in use on hundreds of paper and board machines worldwide.