Prinova Digital - Perfect for Digital and Offset Productions
News General news
With the Prinova Digital, Muller Martini is launching an impressive new solution for digital saddle stitching. The hybrid saddle stitcher, which produces at 9000 cycles per hour, is not only perfect as an entry-level model for digital saddle stitching, but also processes conventionally printed jobs confidently and reliably.
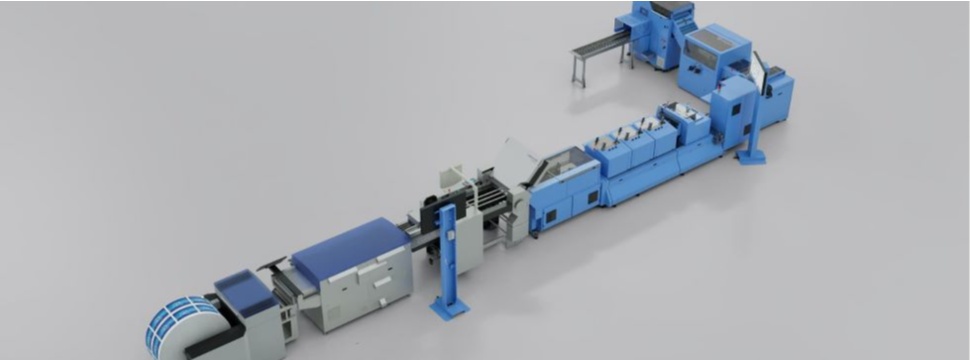
The Smart Factory is no longer just about softcover and hardcover products. Saddle-stitched magazines, brochures and catalogs are also increasingly being printed on digital presses. To produce these short runs efficiently, cost-effectively and, as far as possible, without manual intervention, a completely automated workflow is needed from prepress to the finished end product. This is what the new Prinova Digital saddle stitcher offers – the fascinating hybrid solution for entry-level digital saddle stitching and the stitching of conventionally printed products.
With the Prinova Digital, print shops are equipped for the challenges of the future, which offers them a high level of investment security. This is because the saddle stitcher, with its good price/performance ratio, is ideal for businesses that run conventional offset production alongside purely digital products, or produce combined hybrid products ("offset/digital mix"). With the flexibly configurable system, individualized or personalized print products can be produced efficiently and in high quality, down to run length 1 – and always with variable product thickness.
High automated saddle stitching
The completely redesigned pass-through folder is the link between the digital feeder and the saddle stitcher. Equipped with the latest operating technology, Asir PRO camera, and a completely new infeed that can now also be equipped with creasing, it is the technical highlight of the Prinova Digital.
The stitching machine of the Prinova Digital also adapts to the product thickness and controls the stitching wire length fully automatically from product to product. The automated wire feed gear has now been installed outside the stitching center, which significantly improves operability and accessibility. The three-knife trimmer also adjusts automatically to the product thickness. Cutting takes place with the product stationary, which guarantees the highest cutting quality.
Innovative operating concept
The Prinova Digital has an intuitive control system. Its new user interface with context-sensitive displays and innovative operating concept increases user-friendliness – which in turn shortens processes. Settings on a large touchscreen are made centrally instead of selectively. In addition, up to two external screens are available for displaying production data and thus a perfect overview of the production process. In the case of digital production, the workflow view clearly shows the next job on the reel, which formats are pending, or whether waste has occurred. This means that operators always know where they stand with their jobs.
Efficient short(est) runs
Muller Martini redeveloped the entire feeder section on the Prinova Digital. It now has individual feeders with servo drives. The up to 14 individual feeders (ideal for hybrid production), which can be easily operated by a single employee thanks to their high loading height, can be tilted. They thus enable several application options at the same time, such as manual loading or setting the perfect discharge height for signatures. This means that the saddle stitcher can be changed over much more quickly and short (or long) runs can be produced much more efficiently. The Prinova Digital thus offers a clear efficiency advantage over other saddle stitchers in this performance class.
High quality end products
In addition to motion control technology and the associated faster make-ready processes, the highlights of the new Prinova Digital saddle stitcher also include the new Asir PRO camera system developed by Muller Martini. This recognizes and compares the printed sheets using 1D/2D code and/or image comparison. Faulty end products are thus finally a thing of the past.