Kirk Group rides packaging reshoring wave with KODAK FLEXCEL NX Technology from Miraclon
News General news
“We approach a new packaging technology today in exactly the same way we have for 50 years. If it looks useful, we investigate it, and if it stands up to scrutiny, we integrate it, validate it, and take it to the market.”
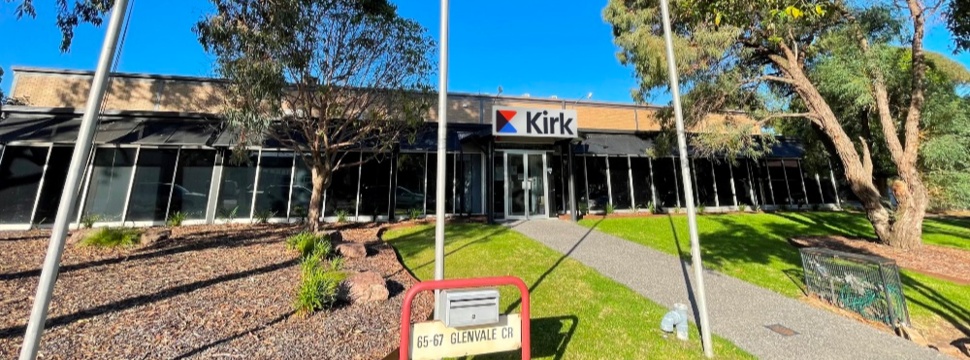
John Kapiniaris, General Manager of Australia’s Kirk Group, the largest provider of graphic arts services and image carriers in Australia and New Zealand, is providing context for the group’s latest technology acquisition — KODAK FLEXCEL NX Central Software, the new automated plate layout technology from Miraclon, which he says has “transformed our plate utilization efficiency.” FLEXCEL NX Central Software enables the integration of multiple advanced plate surface patterning features - including those delivered within FLEXCEL NX Print Suite for PureFlexoTM Printing - into one automated plate layout, and increases consistency and reduces errors by minimizing operator touchpoints. It also improves productivity by enabling multiple users on the network to remotely view or manage the plate layout process.
Early adoption of technology is a Kirk trademark — “Innovation is in our DNA,” says John — and a major reason for its success over the 50 years since Graeme Kirk founded the business in 1972, initially to provide artwork services and gravure cylinder engraving. The company moved into flexo in the 1980s and 1990s and today has four manufacturing sites in Australia and New Zealand — Sydney, Melbourne, Brisbane and Auckland — and, since 2020, a presence in Mumbai, India.
Fast movers
“We aim to always be first to market,” says John, before explaining how rolling out a new technology involves working closely with “a trusted network of suppliers and customers to really field test a solution.” The company’s adoption of FLEXCEL NX Technology in 2010 is a good example of this combination of technological curiosity and close collaboration, as John recalls. “It was one of our trusted customers that alerted Graeme to a groundbreaking new technology. He immediately investigated, liked what he saw and bought a FLEXCEL NX System. Following the new technology install, we worked with a major brand and our trusted print partner to qualify the technology across their product range, evaluating it on multiple SKUs with really complex designs — multiple colors, fine text, and so on. At the end of the qualification process we knew, and so did the brand owner and printer, that we had something genuinely new and exciting to take to the market.”
Reshoring boosts local demand
FLEXCEL NX Central Software is Kirk’s third recent investment in Miraclon technology, following the November installation of a KODAK FLEXCEL NX Ultra Solution and investing in the FLEXCEL NX Print Suite for Flexible Packaging to access PureFlexoTM Printing Technology before that. They are all in line with the company’s policy of systems- and technology-driven innovation. The solutions add enhanced capabilities to Kirk’s offering — more efficient plate utilization, sustainable plate processing, and on press efficiency — which are vital to the company’s response to what John Kapiniaris describes as “resurgence in local demand in the wake of the pandemic, as many brands bring packaging production home from overseas.”
“The pandemic caught a lot of brands off guard,” he continues. “For the best part of two decades the trend has been to ‘offshore’ packaging on cost grounds. That’s understandable if the supply chain is stable, but the disruption in 2020 forced brands to reconsider the strategy. Do they stay offshore and risk interruption in supply, or re-partner with local suppliers? Judging on the increased volumes we’re handling, the answer is to come home! We’re seeing work returning that left ten years ago, and over the last 12 months there’s been a flurry of investment in new flexo presses among our customers.”
This returning business enhances what was already a positive outlook for Kirk’s flexo prepress services, demand for which has grown strongly over the last decade, reflecting flexo’s steady advance at the expense of gravure. Says John: “Flexo gives brands the agility and flexibility they need in marketing campaigns, and since the advent of FLEXCEL NX Technology, the levels of quality and consistency to match gravure and litho.”
Automation controls costs
Welcome as the reshoring of packaging production is, Kirk is conscious that the reason it went overseas in the first place — cost — remains an important factor in brand owners’ calculations. “Automating processes wherever possible is central to our strategy,” says John, citing as an example the ‘Flite’ print management system Kirk launched in 2019. “Flite automates all the steps from final artwork to delivered plates, removing manual touchpoints and connecting all stakeholders in a transparent production environment. We build a customized workflow for each customer, based on an in-depth understanding of their business requirements, volumes, color strategy and printer space. It takes away all the daily ‘noise’ — the phone calls, emails, status requests, and so on, and creates a highly dynamic environment, working in real-time.”
FLEXCEL NX Central Software is the latest string added to Kirk’s bow. Developed by Miraclon specifically to support customers in their drive for efficiency, waste reduction and labor savings, the software is tailored to the FLEXCEL NX System and enables the automation of all plate production, including the automatic application of multiple advanced plate surface patterning features.
John Kapiniaris says FLEXCEL NX Central Software has increased plate utilization by upwards of 5% — delivering more saleable plates and resulting in greater sustainable operations.”
Dynamic plate layout “the biggest benefit”
He adds, however, that the biggest benefit from the platform is “the ability to maintain a dynamic plate layout right up until the last minute, which is a real game-changer in the Just-In-Time packaging business. FLEXCEL NX Central Software essentially allows us to hold a live ‘bucket’ of jobs until we’re ready to process the plates. Effectively, it gives us an extra six hours in which we can accept last-minute jobs, that are automatically added to the plate layouts, maximizing the plate utilization, and that’s a big boost to capacity and efficiency.”
FLEXCEL NX Central Software is also improving Kirk’s plate delivery infrastructure. Says John: “Before, we operated a centralized system with one department preparing plate layouts before sending them out to each site. Now sites have their own ‘bucket’ into which we deliver files, which are automatically laid out and output when required. It’s a local, more dynamic approach that lets us turn plates around faster.” He adds that, in an unexpected bonus, FLEXCEL NX Central Software is opening up a new market for Kirk among narrow web label printers. “Turnaround times in the sector are near-instant, and competition is fierce. Keeping plate layouts fluid, and with utilization more predictable, it allows our business to become highly competitive in this market.
High expectations
Kirk also has high expectations of the FLEXCEL NX Ultra water-based processing solution that is currently being rolled out to customers seeking more sustainable plate solutions. Solvent-free and VOC-free, the FLEXCEL NX Ultra Solution features the patented Miraclon-developed KODAK Ultra Clean Technology, and is the first aqueous solution that produces consistent, high-performing plates in a high-volume, low-maintenance environment.
“When we saw the FLEXCEL NX Ultra Solution in action, it was another example of one of those ‘lightbulb moments’ you get from Miraclon,” says John. “We’ve been exploring water-wash processing for a while because it supports the importance of sustainable manufacturing for many brands. This included acquiring a business a few years ago that was active in the space with different technology, so we’ve gained a good understanding of the issues. However, the FLEXCEL NX Ultra Solution gives our customers the quality and consistency associated with FLEXCEL NX Technology, and that’s an attractive combination. It’s another case of Miraclon being that one step ahead of the market.”
He cites PureFlexo Printing as another example of the manner in which Miraclon incrementally advances flexo’s capabilities. Kirk invested in the solution in 2021, initially working with the Miraclon R&D team to address a specific customer issue, but also saw improvements with consistency, reducing the frequency of adjusting the color profiles. Says John: “PureFlexo Printing quickly became our default solution for all flexible packaging customers, who are achieving quality and consistency levels that have amazed and excited brand clients.”
The use of PureFlexo Printing has improved the predictability of the print on press, with less unwanted ink spread and the associated defects traditionally accepted as part of flexo printing. This has allowed our team to focus on bringing additional capabilities and value to our brand and printer clients and spend less time addressing traditional flexo challenges.”
Trusted partners
They didn’t know it at the time, but the customer that suggested Graeme Kirk look at FLEXCEL NX Technology in 2010 was setting in motion a remarkably close collaboration between Kirk and Miraclon that continues to the present day. For John Kapiniaris it’s a “truly open two-way partnership from which we’ve both gained beneficial outcomes. It’s based on trust — we appreciate that Miraclon trusts us to be involved in alpha- and beta-testing new developments and values our feedback. And the trust goes the other way — we welcome Miraclon dealing directly with our customers if it will help us all arrive at the right solution.”
Healthier discussions
Perhaps the greatest compliment he pays Miraclon is his take on how FLEXCEL NX Technology and its successive iterations has, in his words, “enabled healthier discussions around the return on investment of the job. Before, it was all about who had the cheapest plate, but the arrival of FLEXCEL NX Technology changed that, not least because the advances it represents encouraged other players in the flexo process to up their game. That changed the discussion to the overall cost of a job — how factors like color strategy, plate patterns, aniloxes, press conditions, operators’ capabilities all contribute to the total output and the impact of the packaging on the shelf. That thinking has transformed the industry.”