Innovation, collaboration and KODAK FLEXCEL NX Technology drive growth for Impression Label
News General news
Early in 2022 a new name — Impression Label — appeared on the label manufacturing scene in Denver, Colorado (US). The rebranding followed the merger of two long-established Denver label manufacturers, Blair Labeling and Buckley Graphics, which, says Chief Financial Officer Marco De La Vega, “created a single company with over 350 years’ combined experience, committed to providing Colorado manufacturers with truly innovative solutions in product design, printing and packaging.”
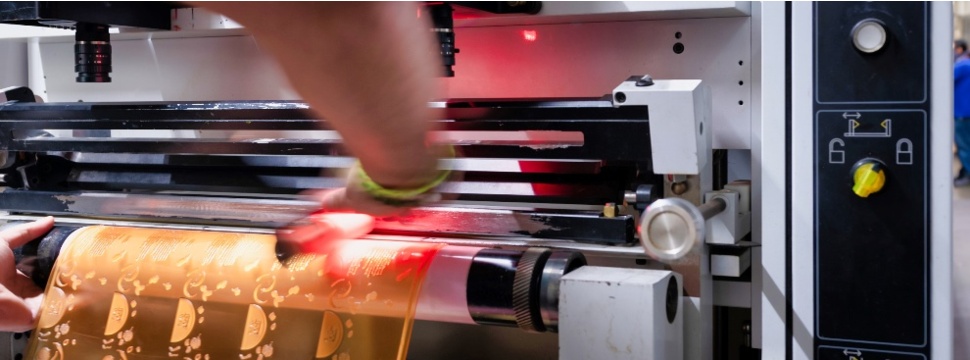
In their latest major development, Impression Label has now upgraded its complete prepress set-up with KODAK FLEXCEL NX Central, the new automated plate layout software from Miraclon. The investment comes after extensive beta-testing of the technology, during which Impression achieved significant time, material and cost savings, including eliminating up to an hour per day on time spent manually preparing plate layouts, and significantly boosting plate utilization.
Surprising beginnings
Marco and his brother Christian, Impression’s Chief Operating Officer, vividly remember their entry into the pressure-sensitive label business. “After all these years, it seems like yesterday when my mother called us and said she’d bought a label printing business,” he says with a smile. “As her background was in biochemistry and she and our stepfather were newly retired, this was a slight surprise.”
The year was 2008, at the height of global financial crisis, and the brothers’ mother, Lourdes Solis, was seeking a relatively safe investment in manufacturing. Recalls Marco: “Along with my stepfather, Spencer Brown, they looked at around 180 businesses before settling on Blair Labeling, taking the view that labeling was growing and appeared to be pretty recession-proof.”
The acquisition made the company one of the largest 100% minority- and women-owned businesses in the US and signaled the start of a period of strong investment and growth under the leadership of Lourdes, Spencer, Marco and Christian. Today, Impression Label offers design-to-delivery production of a wide range of high-quality pressure-sensitive prime, promotional, and industrial labels, including decals, tamper-evident constructions, thermals, patterns, tags, hangers and card products. The company’s principal markets are chemical agriculture, food supply and nutraceuticals.
One thing that makes Impression Label different from similar businesses is the strong cooperative, collaborative culture that’s apparent among the 33 employees. “We have a very flat structure,” explains Marco. “It isn’t based on a rigid hierarchy, but on a ‘How can we get this done?’ approach to every job. Whatever needs doing, we show up and get it done. There are three things we aim to deliver — competitive pricing, high quality products and great customer service — and we like to think we’ve got them all covered.”
FLEXCEL NX — “The best technology for the business”
Impression Label was an early adopter of the KODAK FLEXCEL NX System, installing the technology in 2008. “We checked out other HD flexo plates on the market,” says Christian, “but FLEXCEL NX Technology was clearly superior from both a productivity and quality perspective. Print consistency and quality were there from the start and have been enhanced over time with DIGICAP NX Patterning and NX Advantage. The FLEXCEL NX Plates are far more durable than competitors’, which matters to us — especially when we’re regularly running huge-footage jobs. The technology is also very user-friendly and forgiving, something Marco and I can vouch for as relative newcomers to press operation.”
Impression Label is a 100% FLEXCEL NX Plates business, says Marco. “The technology is crucial to our high-quality proposition, which is important given the growing trend for customers to want high impact labels featuring foil and metallic finishes. We run reverses, flood coats and a lot of white, with up to seven colors registered over it. The whites we lay down look like they’ve been rotary-screened. All without any issues.”
A step-change in productivity with KODAK FLEXCEL NX Central Software
As well as the time and cost savings, the software’s automated layout optimization contributes to users’ sustainability goals by creating less waste and using less energy and solvent. It seamlessly enables the integration of multiple advanced plate surface patterning features, designed to enhance print performance, into one automated plate layout, and increases consistency and reduces errors by minimizing customer touchpoints. It also improves productivity by enabling multiple clients to remotely manage the plate layout process.
FLEXCEL NX Central Software simplifies and automates
Marco De La Vega describes the benefits Impression Label is getting from the new software: “Previously, our art department spent a lot of time getting the best fit of jobs on the plate. Now, with FLEXCEL NX Central Software, it’s all automated; it takes out the guesswork and optimizes plate layouts. It allows us to get the most out of our spend on plates and free up our prepress managers’ time to focus their expertise elsewhere.”
Art department manager Kate Pooch speaks from her daily experience of the improvements that the new software platform has brought to Impression Label. “FLEXCEL NX Central Software saves us both time and materials and makes the whole operation more efficient. We have two artists in the department, and they generally only used to know the specific jobs they were working on. So, you had to manually drag files over and try to figure out which would make best use of the sheet. Now we just send the files through, and the software lays them out on the plate. It also tells me the percentage of the plate that’s used, so I know if I can keep a plate job open in case another job comes in.” She has the figures to prove the benefits, too: “I estimate we save at least one hour every day, and we utilize around 80% of every plate instead of the previous 60%.”
Kate says an added benefit of FLEXCEL NX Central Software shows itself when the company experiences a power outage. “It used to be that when the power came back on, we had to figure out which plates we’d already made and reload everything. You could even end up making a plate twice. Now, when we boot the system back up, all the files are there. It’s a huge time saver.”
The only customer
Looking back over the 14 years since he and Christian unexpectedly became label printers, Marco gives a lot of credit for the company’s success to the support provided by the Miraclon team. “Every vendor tells you that they’re there for you, but Miraclon really is. And as we’re also a supplier to them, we always aim to deliver the same high standard service. If we ever have an issue, it only takes one call to get a response. The people are easy to work with, and the level of support is unprecedented in my experience. With other large vendors, we feel we’re just a number, but Miraclon makes us feel like we’re their only customer.”