M9 – the new folding dimension from H+H
News General news
Industrialised folding with up to 24 buckle plates
H+H GmbH & Co. KG is unleashing a completely new folding dimension in the multi-plate sector in the shape of the M9. The implementation with up to 24 automated buckle plates and automated fold rollers allows the set-up time to be reduced from several hours to a few minutes; by up to 95% depending on the folding sequence and application type. This ensures that the machine pays for itself within the shortest possible time. Further time-saving features such as the patented slitter shaft cassette, which is also very successfully integrated into MBO folding machines, also increase productivity to the highest possible level. The M9 revolutionises your production of pack inserts!
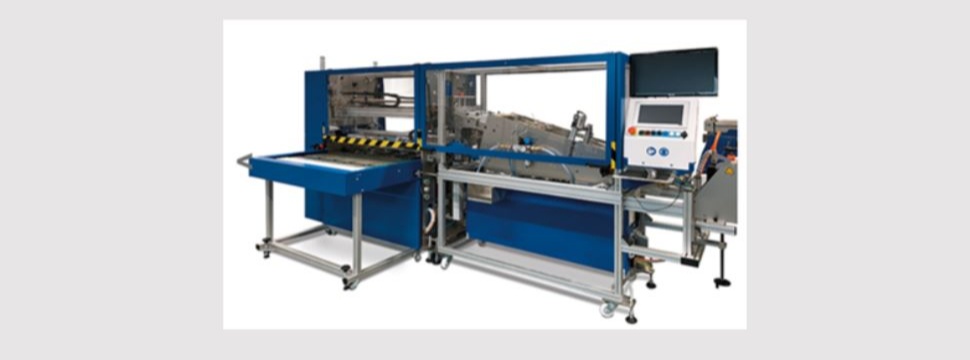
The M9 is designed for a working width of up to 60 cm (23 5/8”) and is suitable for the production of pack inserts for a wide range of fields, such as the pharmaceutical, cosmetics, food and agricultural industries. Here, it is setting a new standard that simply didn't exist before. A further potential application is the production of multi-folded product information leaflets that can be enclosed with small electrical devices, for example.
The M9 is equipped with either 10, 12, 16, 20 or 24 buckle plates. An optional automation package is available. This allows the buckle plates and fold rollers to be adjusted automatically via the touchscreen on the M1 Advanced machine control. In addition, recurring jobs can also be stored. In this way, the set-up time, which can be several hours in machines with this many buckle plates, can be shortened to a few minutes.
The slitter shaft cassette also contributes to reducing the set-up time. These can be removed sideways out of the folding unit. Perfect access is provided to all tools, and they can be changed and set up in an ergonomic working position. The cassette also has two slitter shaft pairs.
The sheets can be fed in either with a continuous feeder or a pile feeder. The alignment path is extra long at 1.8 m (70”) and has an additional belt guide on the right-hand sheet side. This provides optimum sheet alignment. Before the infeed into the fold rollers, there is an integrated sheet ejection system to remove any double sheets. An optional camera system can be installed on the register table for reading codes.
Extensions for the M9
The M9 is equally suitable for parallel fold and cross fold operations. It offers modular expansion options to suit the application in question. The M9 has an integrated conveyor that permits multiple-up production. Inserts produced in multiple-up production, for example, can be pressed out perfectly using the optional PP600 belt press.
A further option is to extend the outsert line. Various cross fold designs and parallel knife folding units cover virtually every folding option. Products can be sealed either using a cold glue system or a sealing labeller.
The SmartPACK100 is used to check the folded outserts against all relevant quality criteria with a camera system. Imperfect products are ejected into a lockable container. This avoids products being intermixed. The automatic filling of the trays with the folded pharmaceutical pack inserts completes the perfect production line. As an option for the SmartPACK100, the M9 can also be operated with the manual XP-D250 delivery, for example.