When good experiences become even better: DZZ Druckzentrum Zurich commits fully to the KODAK LIBRA VP2 Digital Plate
News General news
The new KODAK LIBRA VP2 Digital Plate for newspaper and commercial offset has just been launched in the market by Kodak.
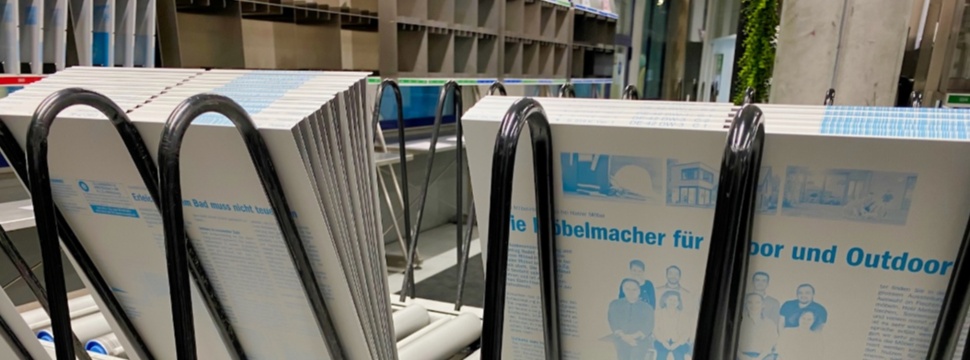
Who could be better suited to report on the new violet plate’s capabilities in production than a user who habitually prints high volumes, demands high performance and already has experience with the predecessor LIBRA VP as well as violet plates from other manufacturers? DZZ Druckzentrum Zurich is operated by Tamedia, a privately owned Swiss media company which is part of the TX Group, and has been producing exclusively with the new KODAK LIBRA VP2 Plate since Q3 of 2019.
Center of excellence for newspaper and promotional printing
As Switzerland’s largest and most productive newspaper printer, DZZ churns out around ten million daily and weekly newspapers, customer magazines and commercial products per week, which roll off the presses 24/7 in three-shift operation. Production takes place on a Koenig & Bauer Commander 6/2 web press line consisting of five 72-page printing units. Apart from Tamedia newspaper titles like the Tages-Anzeiger, the portfolio also includes a free commuter newspaper called 20 Minuten as well as numerous products on behalf of external customers such as Blick, Neue Zürcher Zeitung, various Swiss Regiomedia newspapers and Migros Magazin. The printing center gets through approximately 1.3 million offset plates annually, the majority in 317 x 482 mm single format.
Stefan Abbt, Deputy CEO and Head of Newspaper Production at DZZ, lists the following plate features as being particularly important to his company: “We need long run lengths. The ability to manage with a single set of plates, even for very long individual runs of 200,000 copies, is a must for us. A uniform plate coating, consistent dot sharpness and uniform ink transfer throughout even the longest runs coupled with high quality prints are other key aspects.” Kurt Pechlaner, CTP / Plate Production Manager, adds: “We also set great store by clean and burr-free cut edges, so that no ink can build up there and show on the print and the offset blankets don't wear out too early.”
Kodak violet plates in use successfully
The Zurich newspaper printer was already deeply impressed by the results achieved in extensive CTP and printing tests with LIBRA VP, Kodak’s previous plate with a violet sensitive photopolymer coating. “We were very happy with LIBRA VP’s price and performance from the word go, which is why we made a complete switch from another vendor’s product to Kodak’s violet plates in March 2018,” says Abbt.
When DZZ was invited to beta-test the LIBRA VP2 Plate in May 2019, they jumped at the opportunity because, as Abbt puts it, “We were hoping for stability improvements as well as longer cleaning intervals for our plate processors. The trials were supported on-site by a Kodak expert in what proved to be a very effective partnership. LIBRA VP2 delivered these hoped-for advances, as daily use has confirmed ever since we migrated totally to the new generation of the Kodak violet plate.”
LIBRA VP2 Plate lives up to its promise
The plates are made on three violet CTP lines, each of which achieves a maximum productivity of 240 plates per hour. This high throughput is regularly taken advantage of during the daily prime time period from 9 to 11.30 p.m. Together with the new KODAK COF-2 clean-out finisher, the LIBRA VP2 Plate has substantially improved the processing step – for which DZZ uses conventional plate processors with the prewash station switched off. “The plate processors no longer get so dirty and we spend far less time on cleaning,” Pechlaner comments. “What’s more, the clean-out finisher now lasts for 4000 square meters of plates rather than 2500 with the same amount of replenisher before it needs replacing. That’s a real step forward that also represents an improvement in terms of sustainability.”
Regarding the performance of the LIBRA VP2 Plate in production, Abbt testifies to the high print quality both on different papers and with the 150 lpi AM screen which is used for all products. He sums up the situation as follows: “LIBRA VP2 is significantly more robust and stable, and the printing process as a whole is much smoother. In view of the improved stability and the time we save on cleaning in the platemaking department, we’re one hundred percent in favor of this plate and we’d give it top grades on every account.”
It is therefore only logical that the Centre d’Impression Lausanne in western Switzerland recently became the latest Tamedia plant to opt for production with the LIBRA VP2 Plate on its Wifag newspaper web press.