KODAK PROSPER Plus Imprinting Systems offer packaging printers digital flexibility and adaptability in an ever-changing marketplace
News General news
Digital printing is establishing itself in more and more segments of packaging production, driving growth in flexible packaging, folding cartons, corrugated boxes and labels.
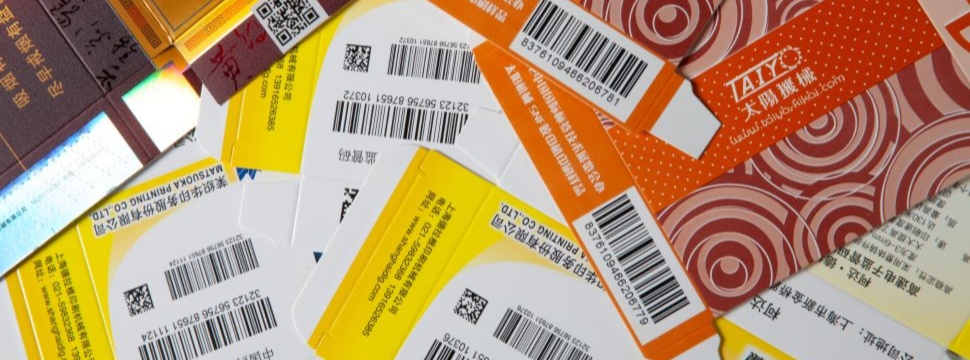
Packaging printers and converters are using the technology to produce more agile, efficient and cost-effective solutions to better meet the needs of brand owners as well as e-commerce platforms and retail chains.
The demand for faster time-to-market drives the spread of digital printing in packaging applications because the long lead times and upfront costs of platemaking or preparation of cylinders for analog printing processes are eliminated. Brand owners are constantly looking for solutions to support more frequent design changes and cost-efficient short-run production, therefore needing greater flexibility. Brands are also looking for personalization and versioning of packaging to foster consumer engagement and drive business success, such as code-based sweepstakes or connected, smart packaging applications. These attributes contribute to packaging printers’ return on investment by creating new opportunities, increase revenues, and highlighting competitive advantage.
Given these usage options and application benefits, it is no surprise that digital packaging printing is predicted to grow at an average annual rate of over 5% globally from 2023 to 2033.
Digital imprinting for impressive packaging
In addition to fully digital packaging presses or specially designed hybrid presses, there is another option for making packaging printing digital: the integration of digital imprinting systems that can match quality and printing speeds onto existing conventional equipment. This allows for a solution that is 100% tailored to a packaging converter’s needs and breathes new life into their existing equipment without having to make a huge financial investment.
An outstanding example of this is track and trace applications that utilize serialized QR or 2D codes for product and brand protection, as well as support anti-counterfeiting measures, such as those provided by KODAK PROSPER Plus Imprinting Systems. Kodak's PROSPER Imprinting System portfolio features high image quality and high-speed solutions. The systems use KODAK Stream Continuous Inkjet Technology, which enables high speed and high ink coverage on glossy substrates thanks to precise, round drop placement.
KODAK PROSPER Plus Imprinting Systems were designed for integration into flexo, gravure and offset packaging presses and packaging converting machines such as folder gluers. The versatile imprinting solutions are suitable for corrugated, folding carton, label and flexible packaging applications. With their fast speeds of up to 600 mpm, PROSPER Plus Systems rule out any impairment to analog packaging production equipment productivity as a result of the digital component.
PROSPER Plus Systems provide up to 600 x 900 dpi resolution and produce image quality that is difficult to distinguish from traditional printing. The print width of the base configuration is 105 mm; CMYK color printing is enabled by cascading four of these inkjet modules. The systems are available in different speed and width versions, allowing the converter to customize the solution to fit their business needs.
Going wider: Built-in flexibility
PROSPER printheads can be configured up to 12 across, creating a customized solution to fit the needs of a large variety of applications. With exceptional scalability, packaging printers can start small, then add additional imprinting heads with a field upgrade. Depending on the configuration, systems can include up to 12 print stations and 24 printheads and can be easily integrated into existing equipment using Kodak or third-party solutions. Printers can start with monochrome printing and later add spot and process colors as their business needs evolve.
The significant role of inks and primers
PROSPER Plus Imprinting Systems employ water-based pigment and dye-based KODAK EKTACOLOR Inks developed and manufactured by Kodak, which dry fast owing to their chemical composition. A key advantage of the inks lies in Kodak’s proprietary pigment micro-milling process which creates extremely fine nanoparticulate pigments with a very narrow size distribution. The finer pigments make the ink easier to jet, reduce light scatter to achieve richer and purer colors, and deliver a superior color gamut as well as ultra-thin dried ink layers.
In addition, Kodak’s inkjet inks differ from competitive inks by having a lower level of humectants. This results in faster drying, even when printing with high ink coverage on difficult substrates. All of these benefits of EKTACOLOR Inks enable PROSPER Plus Systems to print vivid images with vibrant colors and reliably render the offset color gamut. Packaging printers also benefit from the fact that Kodak offers not only CMYK process color EKTACOLOR Inks but also customized spot color inks. This means, PROSPER Plus Imprinting Systems users can accurately reproduce brand colors and more easily meet the color expectations of brand owners.
One particularly important aspect as far as packaging is concerned is that EKTACOLOR Packaging Inks may be used on the non-food-contact side of paper, paperboard and film packaging intended to contain dry foods and when used as intended may be properly considered “safe” in accordance with the following legal and industry requirements:
- US Federal Food, Drug, and Cosmetic Act and applicable food additive regulations (21 C.F.R. Parts 170 et. seq.)
- Canadian Food and Drug Act and the Canadian Food and Drug Regulations (C.R.C., c. 870 Part B, Division 23)
- Article 3 of EU Framework Regulation No. 1935/2004 and do not pose a health or safety risk when printed on the on the exterior, non-food-contact side of paper and paperboard packaging for dry foods
- Good Manufacturing Practices (GMP) of the European Union, EU Regulation No. 2023/2006
- EuPIA (European Printing Ink Association) Exclusion Policy for Printing Inks and Related Products 4th Edition
- Annex X of the Swiss Ordinance on Materials and Articles in Contact with Food (SR 817.023.21)
- Nestlé Guidance Note on Packaging Inks, October 2018
- Annex A of the Indian Standard IS 15495:2004 “Printing Ink for food packaging – Code of Practice”
PROSPER Plus Imprinting Systems also benefit from water-based, ink-receptive KODAK OPTIMAX Primers that are optimized for EKTACOLOR Inks. In addition to creating a thin layer to increase ink adhesion, the primers immobilize the pigment, allowing high-speed printing even with high ink coverage. Just like EKTACOLOR Inks, OPTIMAX Primers do not contain any volatile organic compounds (VOCs) or environmentally hazardous substances, which benefits sustainability. OPTIMAX Primers improve sustainability even further by facilitating deinkability, thus increasing the recyclability of paper and fiber-based post-consumer packaging materials.
Kodak has designed a range of high-performance OPTIMAX Primers for a wide range of substrates and applications. These include an OPTIMAX Standard Primer for uncoated papers and an OPTIMAX Enhanced Primer for coated papers. OPTIMAX Packaging Primers are available for uncoated and coated corrugated and folding carton packaging applications, as well as for non-absorbent substrates such as plastic, film, and materials for personal care products.
A complete digital solution with customized integration from a single source
PROSPER Plus Imprinting Systems are comprised of printheads, data and fluid controllers, EKTACOLOR Inks and dedicated OPTIMAX Primers. Kodak has a wealth of expertise in the engineering and manufacturing of inkjet towers and mounts for the effective integration of imprinting systems into analog printing presses and packaging converting lines. This allows Kodak to quickly provide each customer with a custom-engineered solution to enable practically any digital packaging application.
“With PROSPER Plus Systems, packaging printers can implement hybrid solutions in a very flexible and cost-effective way, allowing high-quality printing on sometimes difficult substrates without compromising the productivity of the entire production line. Our imprinting systems facilitate the implementation of innovative ideas that change the way packaging impacts consumers,” said Randy Vandagriff, Senior Vice President, Digital Print, Kodak. “As a single-source supplier of the total solution, including imprinting systems, inks, primers and integration solutions, we can respond quickly to changing requirements in the development of inks and primers as new packaging substrates are launched.”