KODAK PROSPER 7000 Turbo Press: High-Speed Inkjet in a Class of its Own
News General news
High-Speed Inkjet is seen as the technology that can transform printing from traditional analogue printing processes - most notably offset - to digital production, even well above short-run production.
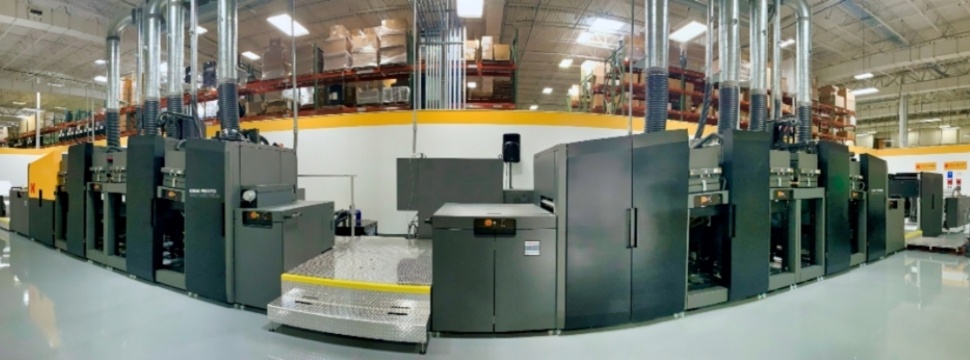
Currently, there is no other press on the market to which the term high-speed inkjet applies as much as the KODAK PROSPER 7000 Turbo. With print speeds of up to 410 m/min, it is the fastest inkjet web press in the world for CMYK production printing and a perfect solution for shifting larger print jobs from offset to digital. Kodak designed the PROSPER 7000 Turbo press for high-volume production in a variety of applications.
Turbo speed and flexibility
The PROSPER 7000 Turbo press's wide range of uses is due primarily to its three print modes. They enable the press to print very different applications with an optimal combination of speed and resolution/quality in each case. Turbo mode, with a top speed of 410 m/min, is suitable for applications with low ink coverage, such as transactional documents, direct mail and books. In this mode, the PROSPER 7000 Turbo is capable of reliably producing 34,835 B2 sheets per hour in perfecting mode - almost 35% faster than the next most powerful competitor model. This enables printers to achieve a correspondingly higher turnover with the press day after day. Performance mode, with higher resolution and a speed of 300m/min, is ideal for trade/textbooks, direct mail and other applications with medium colour coverage. Quality mode delivers the highest resolution at a speed of 200 m/min, which is equivalent to offset printing at 70 screens. This mode is suitable for 4c commercial jobs such as direct mail, brochures, catalogues and magazines. Thanks to its enormous productivity in all three print modes, the PROSPER 7000 Turbo press offers an excellent return on investment.
It is easy to switch from one print mode to another. After an initial setup for each mode, all it takes is one click on the press controller, the KODAK 800 Print Manager. This quick and easy change is beneficial for businesses that often need to produce very different applications. The PROSPER 7000 Turbo Press integrates seamlessly with PDF workflows such as the KODAK PRINERGY Platform to maximise operational efficiency. Plus, Kodak's colour expertise with the KODAK 800 Print Manager makes it easy to achieve outstanding colour and image quality right out of the box. An advanced object-oriented colour engine offers sophisticated colour control options, ICC profile support, object-independent screening options and text optimisation.
Two workhorses from the same stud, but with different focus
Naturally, the question of how the PROSPER 7000 Turbo press compares to the recently launched PROSPER ULTRA 520 press in Kodak's inkjet portfolio is of interest, and what the key differences are between the two models. Both are based on Kodak's continuous inkjet (CIJ) technology, which creates a continuously flowing 'curtain' of ink droplets. The printing droplets go directly onto the substrate, while the non-printing droplets are deflected and sent for reuse in the system. Kodak's continuous droplet generation virtually eliminates clogged nozzle modules and maximises press uptime and productivity. Other benefits of CIJ include getting droplets onto the substrate faster than Drop-On-Demand (DOD) technology, so they are placed more accurately for better quality.
The PROSPER 7000 Turbo is designed for high-volume direct mail, commercial, transactional and book printing, while the PROSPER ULTRA 520 is designed for the highest quality applications such as brochures, catalogues, magazines and photo books.
The PROSPER 7000 Turbo uses KODAK Stream Inkjet technology, which enables the very high speeds of this press. The advantages of Stream result from the technology's ability to control dot placement and uniformity extremely precisely at very high speeds. In contrast, the PROSPER ULTRA 520 uses the higher resolution KODAK ULTRASTREAM inkjet technology, thanks to which the press delivers print quality equivalent to 80 screen offset at speeds up to 152 m/min.
Flexibility in substrate types and formats
The PROSPER 7000 Turbo can print on an extensive range of papers in the grammage range 42-270 g/m2, including uncoated, lightweight uncoated and matt, gloss and semi-gloss coated papers. The press's versatility and productivity are supported by its ability to make optimum use of the substrate. Thanks to its maximum web width of 648 mm and printing width of 621 mm, for example, it can print A4 text pages in an arrangement of three-ups in upright format side by side. Alternatively, the web width can be utilised very well for two-up production of A4 pages with bleed in horizontal format.
To reliably produce jobs with high ink coverage on coated papers at the high speeds, the PROSPER 7000 Turbo press has eight intelligent near-infrared (NIR) dryers - four for each side of the web. The dryers are located between the printing stations and are controllable depending on the ink application. Together with Kodak's pigment inks, which have a low content of humectant, this specific drying concept ensures reliable drying of the printed images even with high ink coverage and high web speeds.
Rational operation, intelligent quality optimisation
The cost-effectiveness of a press depends, among other things, on how much manpower it requires. The PROSPER 7000 Turbo requires only one operator for production operation, whose main task is to start and monitor the print jobs. The operator is supported by the camera-based KODAK Intelligent Print System (IPS). The patented IPS ensures peak production performance by continuously monitoring and evaluating system operation. It measures and optimises printhead stitching, colour register and perfecting register, and makes up to five real-time adjustments to image data on each printed page. It also provides a visual monitoring system for operator control. As a result, the press offers reliable production with consistently high quality and minimal waste.
Free choice in pre- and post-press options
To enable fast and reliable production, a digital press should link as seamlessly as possible with post-press. The PROSPER 7000 Turbo has an open architecture for pre- and post-press options. This means that printers can work with a wide range of suppliers of unwinders/rewinders, pre- and post-coating units, rewinders and finishing equipment.
Whether a printer chooses an inline or nearline finishing solution depends on its individual requirements, its job structure and the throughput capacity of the available finishing equipment. Since an inline configuration always carries the risk of having to stop print production in the event of a technical problem in the finishing department, reel-to-reel production and the use of offline or nearline finishing maximises press productivity.
Decades of experience in inkjet production printing ensure perfect start-up assistance
It is obvious that printers entering high-speed inkjet need support in their first steps with the technology that is new to them. Kodak can draw on more than 55 years of experience in installing and commissioning inkjet systems for customers entering digital printing for the first time. With more than 1,600 KODAK PROSPER inkjet systems successfully deployed by printers around the world, the company has extensive experience deploying its technology with customers in a variety of industry segments. Kodak's expertise extends beyond technology to service and training. A comprehensive training and development plan is available for all PROSPER press owners.
With smooth installation, efficient integration into the customer's operational infrastructure and thorough operator training, Kodak's service and support teams ensure that users can get their digital printing business up and running profitably right from the start with the PROSPER 7000 Turbo.