Agility in detailed planning with the Job Optimiser from Koenig & Bauer
News General news
- Advanced planning software for Print 4.0
- Optimisation of costs, makeready and throughput times, delivery scheduling and capacity utilisation based on intelligent job sequence planning
- Maximum planning certainty and transparency
- Straightforward and intuitive use
- Fast MIS/MES integration thanks to cutting-edge interfaces
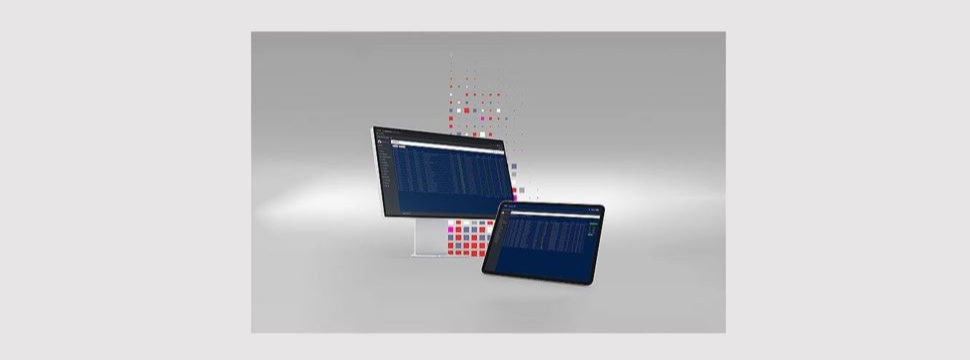
Intelligent production planning is indispensable for modern print companies, given that today’s customers are demanding ever greater product diversity, instant deliveries and lower prices. Agile planning and flexible processes are imperative for implementation of the Printshop 4.0, as they allow companies to react to changing customer demands at short notice and secure a competitive advantage on the market.
With the Job Optimiser, Koenig & Bauer is offering a powerful APS (Advanced Planning Software) tool for the detailed planning of production processes. Intelligent planning and optimisation algorithms automate all planning tasks for maximum planning efficiency. The seamless integration with MIS and MES systems enables print companies to optimise their planning process in the areas of production and logistics, which provides the basis for targeted control over material flows and resource capacities.
Efficient production planning in five steps
Create a perfect production plan faster using automatic detailed planning – the Job Optimiser unlocks efficiency potential in everyday production with the following planning functions:
- The automated importing of pre-planned production jobs from the MIS allows fast and reliable access to all job-relevant information. A job list with a traffic-light assistant provides an immediate overview of the current production status, alongside other information such as material and tool availability, proofs and customer approval. Quick-filter functions allow all jobs that are ready for production to be selected for detailed planning.
- The machine scheduling function defines the machine resources and time windows that are necessary for the individual production steps of the planned jobs. All possible restrictions and dependencies are taken into account in order to ensure that production can be completed on time. Dynamic adjustments to accommodate subsequent changes achieve a high degree of flexibility in detailed resource planning.
- The intelligent control algorithms of the “Load balancing” function enable optimum distribution of the required production steps across suitable presses and post-press machines, providing for uniform capacity utilisation and greater efficiency.
- Job sequence planning determines the order in which outstanding production jobs are handled on the individual machines. The job sequence is optimised according to process- and machine-specific parameters, such as finishing requirements, coating types or the automation features available, in order to minimise makeready times. In the event of changes to the planned jobs, the current sequence and calculated makeready times are adapted accordingly.
- The optimised job list is transferred automatically to the MES software LogoTronic. This ensures both a faster overall process and perfect synchronisation of the individual process steps.
Production planning on an entirely new level
The Job Optimiser is the ideal solution for automated detailed planning in print production. The production sequence is optimised in accordance with process-specific parameters, such as the substrates to be used, the colours involved and finishing requirements, and the significant reductions in makeready time translate to additional production capacities for further jobs. Printing plates, substrates, inks and other consumables are supplied to the relevant machines at exactly the right moment and in precise order.
The Job Optimiser raises production planning to an entirely new. Whether for web-to-print jobs with ultra-short delivery times or folding carton production with a multitude of spot colours and product variants, the Job Optimiser demonstrates its unrivalled performance in every situation: automated job sequence planning, dynamic planning adjustments, and uninterrupted production thanks to reliable resource availability. The Job Optimiser is a powerful and simple-to-use production planning software tool for print companies, and as such an integral element of Print 4.0 for increased efficiency along the entire production chain.