The paper sack: sustainable from raw material extraction to end of life
News General news
Despite inflation and the economic crisis, two out of three consumers attach importance to sustainable packaging, according to the results of a recent study.
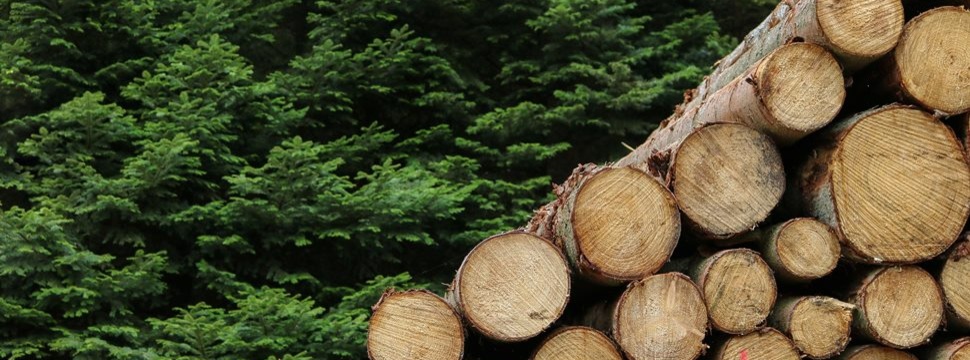
Sustainability is also one of the most important selection criteria for industrial packaging. As bio-based and recyclable packaging made almost exclusively from renewable raw materials, the paper sack has optimal prerequisites. But there is more: the sack paper and paper sack industry is continuously working within all process steps of its production to conserve resources, minimise environmental impacts and at the same time increase product protection - and always has been.
"The creation process of a paper sack begins in the forest, in the case of a paper sack manufactured in Germany primarily in Scandinavian forests" explains Dag Kretschmer, member of the Gemeinschaft Papiersackindustrie e.V. (GemPSI). The term sustainability was coined by the forestry industry: In 1713 it was mentioned for the first time in the sense of a long-term responsible handling of the resource wood. Today's sustainability concept is based on this. One of its principles is to ensure healthy forest growth. Among other things, reforestation, but also thinning, contribute to this.
Everything is recycled
In Sweden, a law was introduced as early as 1903, according to which every tree felled must be reforested. Sweden's forest area has thus doubled in the last 100 years. In Finland, the annual growth of forests exceeds deforestation by 30 %; across Europe, the figure is 25 %. FSC and PEFC are the best-known quality labels for wood. They guarantee that the wood comes from sustainably managed forests. In these forests, trees are selectively felled and for every tree felled, a new one is planted. Regular thinning ensures that strong trees have enough space to grow. In the first instance, dead, weak and misgrown trees are removed. The wood from thinning is used as raw material for paper production, as is process waste from the timber industry such as branches and cuttings that cannot be used for furniture production, for example. "If a tree is felled, every part is recycled, no raw materials are wasted," says Kretschmer. "This principle has always continued in the production of sack paper and paper sacks. In addition to energy-efficient production, our industry always makes sure to generate as little production waste as possible and to recycle and reuse all materials."
Kraft sack paper production conserves resources ...
The production of kraft sack paper is largely energy self-sufficient. 77 % of the total energy demand (heat and electricity) is already generated on site. 89 % of the fuels are already renewable and are used to generate heat, steam and electricity. 81 % of the renewable fuels are by-products of the pulp and paper manufacturing process. For example, the lignin that is extracted from the wood during the cooking of the wood chips is subsequently used as fuel. The steam generated during the cooking process drives the turbines and feeds electricity into the grid, benefiting neighbouring communities. Water is needed in the subsequent stock preparation process. Since the 1990s, average water consumption per tonne of paper has fallen by more than 40 %. This so-called process water is used and cleaned several times before it is almost completely returned to the environment in good quality. If pulp residues accumulate, they are returned to the material cycle. The finished paper webs are rolled up very tightly so that space-saving transport to the paper bag factory can take place.
... just like paper sack production.
Resource conservation is also the order of the day in paper sack production. In addition to the paper, materials that are as environmentally friendly as possible are used, such as water-based inks and starch-based adhesives. The paper is ordered in the exact quantity and size required for each order. Rejects, which can occur in small quantities when setting up the machines, as well as production waste are separated according to type and fed into the recycling circuit. Ink and adhesive residues are stored and used in the next order. Thanks to continuous improvements in paper strength, the general paper consumption per bag has also fallen sharply in recent years. Today, a paper bag for 25 kg of building materials weighs only about 90 g. This leads to considerable cost reductions and the conservation of natural resources. "We always use only as much material as necessary to ensure optimum product protection. This also applies to barrier films," explains Kretschmer. "I am sure that in the future we will have an even wider range of bio-based and recyclable films and coatings at our disposal." In terms of energy management, the company is also constantly looking at how to produce and heat even more efficiently and sustainably, for example by using heat pumps in the production facilities. Thanks to energy-efficient and resource-saving production as well as material reductions, the CO2 footprint of paper bags was reduced by 28% (from 118 g CO2e to 85 g CO2e) between 2007 and 2018. If biogenic emissions and removals were included, it would even be negative at -35 g CO2e.
Sustainable product protection
"When considering the carbon footprint, however, one should not ignore the fact that packaging fulfils an important protective function. The larger ecological footprint is usually the packaged product," explains Kretschmer. "If it is damaged, the damage is greater than if it is protected by packaging. For optimal product protection, the German paper sack industry produces paper sacks that are precisely tailored to the respective product and its special features during filling, transport, storage and use." For example, paper sacks are provided with moisture protection if required to increase their shelf life. Furthermore, they are designed in such a way that no dust is generated during filling and no product losses occur during transport, storage and handling. In addition, thermal valves enable dust-tight packaging and offer a high level of product and tamper-evident protection.
Closing the loop
After their use, paper bags can be easily recycled. According to Prof. Dr. Dirk Burth, Professor of Packaging Technology at Munich University of Applied Sciences, recycling is an effective way to reduce the environmental impact of packaging. GemPSI introduced the REPASACK take-back system in Germany 30 years ago. Every year, more than 20,000 tonnes of kraft paper sacks from industry and commerce are collected, cleaned and then recycled. The fibres obtained are processed into a high-quality secondary raw material and used proportionately with the primary raw material in other paper products such as carrier bags. According to a study by the Fraunhofer Institute UMSICHT, paper bag recycling saved 3,913,200 kg of climate gases in 2021: This corresponds to the average emissions of a passenger car that has travelled around 33 million km. In addition, more than 67,000 t of resources were saved. "In this way, the paper sack makes a contribution to the environment from its creation to the end of its life," says Kretschmer. "Our industry will continue to be committed to making all process steps even more sustainable in the future."