Eticod moves towards higher levels of sustainability with BOBST
News General news
The versatile BOBST MASTER M5 press is Eticod’s weapon of choice when it comes to sustainable flexo printing. The latest version installed, one of four in total, features highly automated technologies and UV LED curing, helping to reduce energy consumption and ensure consistent, high quality and exceptional productivity for the Polish label company.
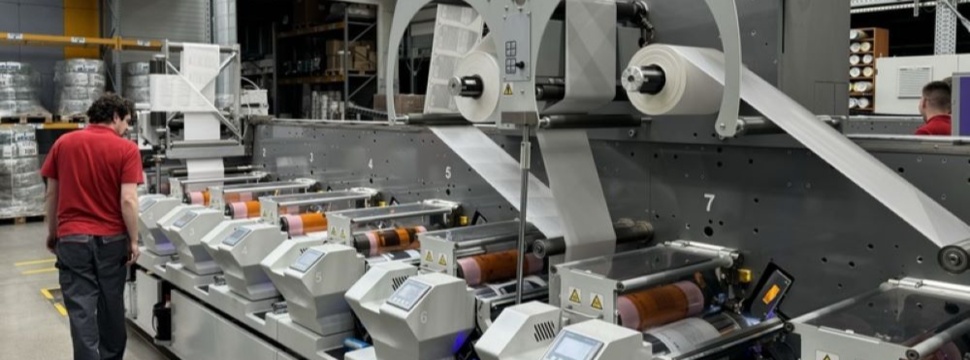
A leader in the production of labels for national and international clients, Eticod is located in Katowice, in southern Poland. Established in 1994, the company has a long history of working with BOBST printing presses. The current production floor is home to four MASTER M5 inline flexo machines, two equipped with traditional mercury lamps and two utilizing advanced UV LED curing technology. Supplied by Rotary, BOBST’s agent in Poland, the machines produce labels for many types of markets, such as food and beverage, beauty and personal care, as well as automotive, oil and various industrial sectors.
Eticod is managed by the son of the founders, Aron Huc, who serves as Vice President of the Management Board and Co-Owner. He explained the preference for BOBST technology, saying, “The incredible versatility of our BOBST MASTER M5 machines allows us to print a huge variety of labels, including multi-layer and highly embellished labels, but also shrink sleeves and many other kinds of applications, in both short and long runs.
“BOBST technology enables Eticod to produce beautiful designs and complex labels while also reducing waste,” he added. “Our operators can control the press digitally, while the in-line inspection system identifies errors and automatically locates faulty labels on the re-winder. And that all happens in one single pass, which saves a lot of time.”
Eco-friendly printing with BOBST flexo
Aron’s parents have passed on their great passion for environmental responsibility. “With the second generation managing the company, we want to take even bigger steps towards sustainability. I’m tired of greenwashing and I want to make a real difference! And now that Eticod employs over 130 staff and operates 24/7, I consider it my responsibility to do just that,” he stated emphatically.
Through a number of eco-conscious initiatives, Eticod is continually developing according to this sustainability agenda. The modern facilities, built in 2015 with extra thick walls for insulation, are entirely lit by energy-efficient LED lighting. None of the 11 printing presses are fitted with chillers. Instead, the energy created by the machines is cleverly used to heat the building; even the tarmac in the car park is warmed up during the winter to stop the snow from settling.
“Of course, a key area for making our business more sustainable is through the printing process itself, which is why we specified our two latest BOBST M5s with UV LED curing,” said Aron. “We also work with our customers to create the most eco-friendly solutions for them, offering different types of substrates and embellishment options.”
As Eticod has experienced, the MASTER M5 inline press fully digitalizes the production workflow. With reduced downtime and low waste in the process, coupled with energy-efficient and fast LED curing, this technology offers a much more sustainable flexo operation. The high level of automation on the press also makes it easier to run for less experienced operators, supporting them with fast setup times while ensuring productivity and process repeatability. Very high press uptime, very fast time-to-market, lower energy consumption and minimal waste make the MASTER M5 a winner for Eticod.
Versatility helps support customers
But there is no time to rest for this label printer. Customer demands for the highest print quality, multiple SKUs and faster time to market, all while ensuring sustainability in all aspects, mean its printing technologies must keep up to speed. Fortunately, Eticod has been able to adapt to these challenges easily, thanks to the flexibility of its BOBST MASTER M5s. One press has recently been retrofitted with two extra print units, a QN booklet label module, and a second Combo laminator and cold foil unit.
“This substantial upgrade to the capabilities of our MASTER M5 means that we can adapt to meet evolving customer demands, allowing us to expand into new applications like shrink sleeves and BOPP. Whenever we have wanted to upgrade any of our presses to cover an even wider range of applications, BOBST has offered us amazing support, helping us to find the right solution,” stated Aron.
“At Eticod, our focus is on providing exceptional service and adding real value to our customers, while building a profitable, sustainable business. And BOBST is an integral part of that journey,” Aron concluded. “I believe that people do business together, not companies. And we feel really confident with the service and support that the team at BOBST provides.”