AquaLine: Voith’s sustainable water management concept for paper production
News General news
-When using a system operated by the AquaLine concept to produce packaging papers, the fresh water consumption is 5.5 to 7 liters per kilogram of produced paper.
-AquaLine Flex brings this figure to below 5.5 liters per kilogram of produced paper by combining a biological treatment plant with filtering systems.
-AquaLine Zero further reduces fresh water consumption to 1.5 liters per kilogram of produced paper, enables complete closing of the water circuits and thereby cuts the effluent volume to zero liters per kilogram of produced paper.
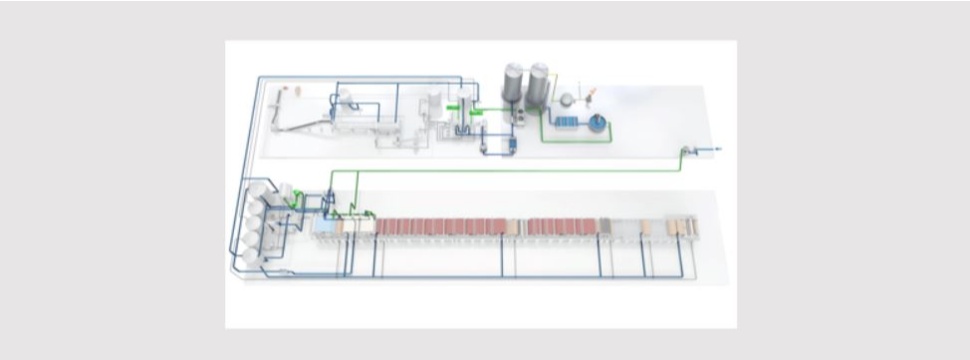
Achieving sustainable reduction of fresh water consumption is one of the key challenges in the development and operation of production facilities. In the field of AquaLine water management, with AquaLine Flex and AquaLine Zero, Voith is introducing two concepts that not only minimize fresh water consumption but, as is the case with AquaLine Zero, can also completely close water circuits.
For the Progroup AG paper mill in Sandersdorf-Brehna, Voith developed the AquaLine Zero concept in collaboration with the customer, delivered it for the first time and successfully commissioned it.
Progroup AG’s aim to keep its use of resources as low as possible without having to compromise production quality has been realized at the plant, which produces 750,000 metric tons of testliner and corrugating medium a year. Approximately 8,500 cubic liters of fresh water can be saved each day with the integrated, closed-loop water treatment plant.
AquaLine and AquaLine Flex
For the implementation of a sustainable water management system in paper mills, Voith has based its AquaLine concept on a water treatment plant with cutting-edge treatment technology that provides for both anaerobic and aerobic biological treatment of process water. With this technology, the fresh water supply per kilogram of produced packaging paper is 5.5 to 7 liters. From this biological treatment plant, between 4 and 5.5 liters of purified process water per kilogram of produced paper is discharged as effluent.
With the AquaLine Flex concept, the next expansion phase of its water management system, Voith can further improve on this result. The additional integration of various filtering systems in the process water circuit of the paper machine enables process water to be returned to circulation. This reduces fresh water supply accordingly. With AquaLine Flex, by combining a biological treatment plant and filtering systems, Voith can limit fresh water supply to below 5.5 liters per kilogram and the effluent flow to below 4 liters per kilogram of produced paper.
Closed water circuits with AquaLine Zero
For closed water circuits with AquaLine Zero, the biological treatment plant operates exclusively via an anaerobic process, the so-called “biological kidney”. All the purified water is returned to the stock preparation process, which means the effluent volume is zero liters. In addition, filtering systems in the process water circuit of the paper machine allow for purified process water to replace the fresh water requirement. This reduces the consumption of fresh water considerably. The exclusively anaerobic process produces a large volume of biogas, which can be used as primary energy, reducing both energy costs and CO2 emissions.
On top of the extra engineering work and greater investments required to operate a paper mill with a closed water circuit, a high degree of operator expertise and process knowledge is also needed.
Our goal is a low COD level in the paper manufacturing process
When treating process water in a biological treatment plant, the top priority is to reduce the chemical oxygen demand (COD) content, which indicates the amount of all substances present in the water that are oxidizable under certain conditions. Fiber slurry, starch and additives are responsible for the COD content in process water. The content is reduced through anaerobic and aerobic stages, and biologically treated water is produced from the process water, which can be returned to the production circuit, thereby conserving resources.
AquaLine and AquaLine Flex reduce running costs and significantly increase the sustainability of the paper mill. At the same time, they contribute to meeting the increasingly stringent environmental requirements in planned capacity expansions, for example. AquaLine Zero ensures the best possible success in the design of new systems. Voith is thereby taking a further step towards increased sustainability and decarbonization in paper manufacturing.