ABB upgrades drive control system at Jujo Thermal paper mill in Finland for improved machine runnability
News General news
- ABB delivered and commissioned upgrade package for existing PM2 drive control system as well as new drives
- Jujo Thermal reports improved efficiency at thermal paper machine
- ABB’s ability to integrate older drives into the new system a key differentiator in project selection
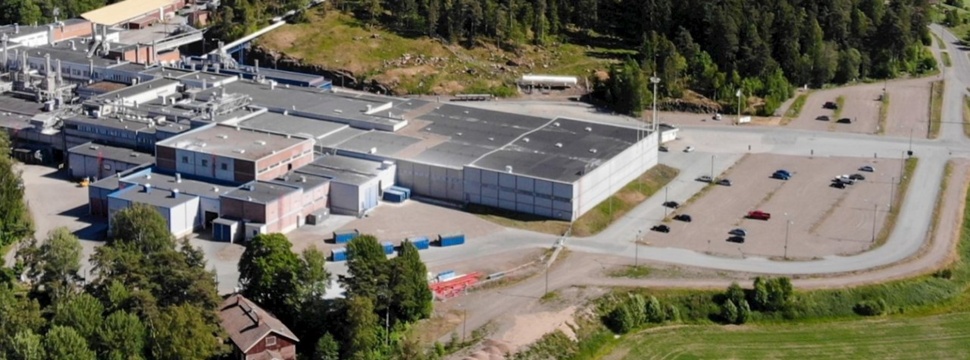
Jujo Thermal selected ABB to upgrade its drive control system at its mill in Kauttua, Finland, for improved runnability and efficiency. ABB’s scope of delivery included the provision and commissioning of the upgrade package for the existing PM2 drive control system and new drives.
Jujo Thermal is one of the world’s leading suppliers of durable, direct thermal papers for labels, tickets, tags and point-of-sales use. It also generates one-side coated self-adhesive label stock and has a production volume reaching 72,000 tons per year.
The project required the team to continue to use some existing, older generation drives. While this increased project complexity as it required experience and knowledge of older systems and devices, ABB was able to leverage its expertise and local project delivery experience to ensure the smooth configuration of the new, enhanced drive system.
“Through collaboration and teamwork, ABB was able to deliver an integrated solution that exceeded our expectations and improved runnability,” said Juha-Pekka Kaivola, Chief Production Officer at Jujo Thermal. “We only wish we had upgraded the system sooner.”
“Jujo Thermal has reported a significant improvement in machine runnability and efficiency since the upgraded PM2 drive control system and new drives were brought online earlier in 2023,” said Sanath Kumar, Global Product Manager, Paper Machine Drives, ABB. “We are extremely proud to be able to showcase our competency in tackling these more difficult projects.”
The renewed system and improved availability will make it possible to increase the annual production of the line. Machine operators can take advantage of the new operating stations and the digital applications integrated into the system.
Among the innovations is the advanced PMC800 datalogger tool, designed to adeptly collect and store meticulously configured data at the millisecond level. This tool proves to be an invaluable asset for fault tracing, allowing comprehensive analysis of historical events whenever the need arises. By leveraging the PMC800 datalogger, the mill can confidently enhance its operational efficiency and bolster its problem-solving capabilities.