Nabe Process Corporation bestätigt die Prozessvorteile von CrystalCleanConnect ein Jahr nach Installation
News Allgemeine News
Automatisches System zur Herstellung von Flexodruckplatten unterstützt Übergang zu nachhaltigerer Verarbeitungslösung
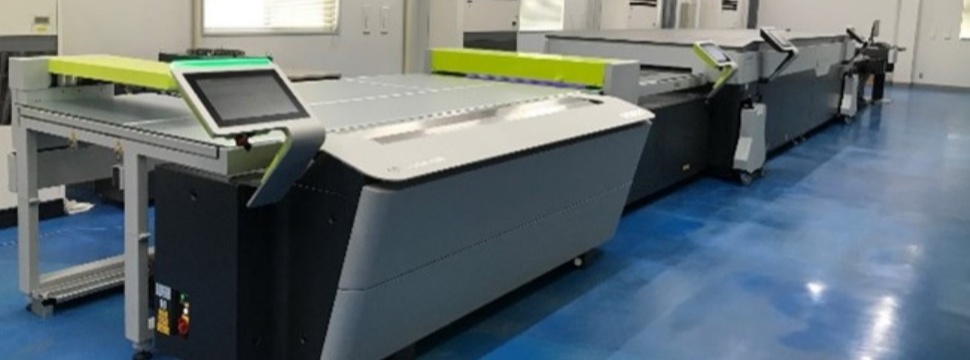
Die Nabe Process Corporation, das weltweit erste Unternehmen, das CrystalCleanConnect installiert hat, wurde 1964 in der Präfektur Takamatsu, Japan, gegründet.
Als das Druckunternehmen in den Flexodruckmarkt einstieg, arbeitete es noch mit lösemittelbasierten Druckplatten und Verarbeitungsgeräten. Im Jahr 2020 begann sich die Nabe Process Corporation jedoch nach einer nachhaltigeren Lösung umzusehen, mit der das Unternehmen neue Maßstäbe für Qualität, Kosten und Zykluszeiten setzen sowie ein besseres Arbeitsumfeld für seine Mitarbeiter schaffen konnte.
Übergang zu einer nachhaltigeren Lösung
„Als wir von den wasserauswaschbaren CleanPrint-Flexodruckplatten AWPTM von Asahi Photoproducts erfuhren, waren wir sofort interessiert“, sagt Yasuo Naka, Flexo Division Manager, Nabe Process Co., Ltd. „Das Auswaschen mit Wasser anstatt mit Lösemittel verkürzt den Zeitaufwand für die Herstellung der Platte deutlich, so dass wir den Durchsatz in unserem Werk verbessern konnten.“
Doch die wasserauswaschbare CleanPrint-Flexodruckplatte AWPTM bot noch weitere Vorteile, wie er betont: „Gegenüber den konventionellen lösemittelauswaschbaren Flexodruckplatten ermöglichen diese Platten eine erhebliche Steigerung der Druckqualität und Produktivität. Darin eingeschlossen sind Kosteneinsparungen und schnellere Zykluszeiten, die durch die kürzere Rüstzeit, die wenigeren reinigungsbedingten Maschinenstillstandszeiten und den geringeren Substratabfall erzielt wurden. Die Flexodruckplatten der Modellreihe AWPTM gewährleisten eine stabile Maßhaltigkeit und ermöglichen eine hohe Reproduzierbarkeit des Druckergebnisses. Da auf Lösemittel verzichtet wird, entfällt die sonst übliche Geruchsbelästigung, was die Arbeitsbedingungen bei der Plattenherstellung sowie im Drucksaal deutlich verbessert.“
Er ergänzt: „Wir sind uns sicher, dass sich unsere Kunden noch mehr über die höhere Qualität und die kürzeren Lieferzeiten freuen werden. Wir werden in der Zukunft mit der CrystalCleanConnect Anlage noch weitaus mehr AWPTM Plattenmaterial für Druckaufträge fertigen.“
CrystalCleanConnect: Die Details
CrystalCleanConnect ist die erste automatische Produktionslinie für Flexodruckplatten, die alle Schritte von der Bebilderung bis zur Ausgabe der montagefertigen Platte ausführt. Dabei werden VOC-basierte Verarbeitungslösemitel durch eine umweltverträgliche Wasserauswasch-Technologie ersetzt.
Das CrystalCleanConnect Gesamtsystem besteht aus den folgenden hochgradig integrierten Komponenten:
- Dem automatischen Software-Hub von Esko, der den Prozess von Anfang bis Ende integriert.
- Einem Plattenladeroboter von Esko. Der Bediener läd das Plattenmaterial einfach in die CDI. Der Roboter transferiert das wasserauswaschbare CleanPrint-Material AWPTM nach der Bebilderung von der CDI in den Crystal XPS von Esko.
- Dem CDI Crystal XPS von Esko. Die integrierte Kombination aus Bebilderung und Belichtungseinheit ermöglicht die lückenlose Kontrolle über die Plattenrückseite und die Druckpunkte mit gleichzeitiger UV-LED-Belichtung auf der Haupt- und Rückseite, um ein äußerst gleichmäßiges und qualitativ hochwertiges Druckbild zu gewährleisten.
- Dem Inline-Plattenprozessor CCC von Asahi mit Trockner und Nachbelichter. Die wasserauswaschbare Druckplatte Asahi AWPTM-DEW muss bei der Verarbeitung mit einer integrierten Luftrakel, die das Wasser von der Plattenfläche entfernt, nicht weiter getrocknet werden. Daraus ergibt sich eine deutliche Verringerung des Zeitaufwands für die Plattenproduktion, denn insbesondere bei Lösemittel- Platten kann die Trocknung bis zu zwei Stunden in Anspruch nehmen.
- Dem Inline-Schneidetisch Kongsberg für eine branchenweit beispiellose Integration. Eine effiziente Verschachtelung der Druckdateien verringert den Plattenabfall um mindestens 10%.
CrystalCleanConnect ist die erste automatische Lösung zur Herstellung von Druckplatten, die das Arbeitsumfeld des Druckmaschinenbedieners verbessert, da keine VOC-basierten Auswaschlösungsmittel verwendet werden. Zudem verbessert sich der Arbeitsschutz, da die Anzahl der potenziell gefährlichen Bedienereingriffe von zwölf auf nur einen Arbeitsschritt verringert wird. Auch stellt diese Lösung eine Premiere in der Druckbranche dar, da sie den Schneidetisch in den automatischen Workflow integriert. Bereits 70 Minuten nach dem Starten des Verarbeitungsprozesses, einschließlich Schneiden, wird die erste Druckplatte ausgegeben.