Wie der Flexodruck neue Verpackungspotenziale erschließen kann
News Allgemeine News
Das gegenwärtige Geschäftsklima ist schwierig, und die Welt der Verpackung macht in dieser Hinsicht keine Ausnahme.
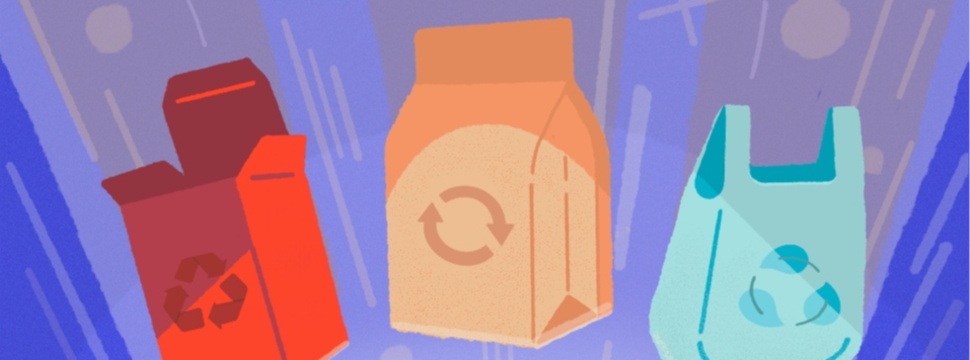
Angespannte Lieferketten, steigende Materialkosten, zunehmende Regulierung, Bedenken in puncto Nachhaltigkeit: Der Branche mangelt es nicht an Gegenwind, und wie alle anderen Sektoren müssen sich auch Flexodruckereien und Verpackungsproduzenten an eine sich schnell verändernde, zunehmend unberechenbare Welt anpassen.
Nach jüngsten Einschätzungen des Marktforschungsunternehmens Smithers sieht die Zukunft des Flexodrucks trotz aller Herausforderungen weiterhin sehr vielversprechend aus. In dem Branchenbericht Die Zukunft des Flexodrucks bis 2027 wird dem Flexodruck ein jährliches Wachstum von 2,1 % vorhergesagt, wobei der Markt im Jahr 2027 ein weltweites Umsatzvolumen von 205 Milliarden $ erreichen soll. Allein im Jahr 2022 soll die weltweite Produktion 449,7 Milliarden Quadratmeter erreicht haben. Der Umsatz mit Flexodruckmaschinen soll bis 2027 jährlich um 1,4 % steigen, und weiteres Wachstum wird aus der steigenden Nachfrage nach Flexodruckfarben, Verbrauchsmaterialien, Druckplatten und Sleeves resultieren.
Wenn es einen Bereich gibt, in dem der Flexodruck auch in den schwierigsten Zeiten florieren wird, dann sind es Innovationen bei Verpackungen. Dieser Aspekt rückt bei Markenunternehmen immer mehr in den Blickpunkt, und hier kann der Flexodruck seine Vorteile ausspielen.
Verpackung mit Priorität
Weltweit ist die flexible Verpackung die am schnellsten wachsende unter den neun von der Smithers-Analyse untersuchten Hauptanwendungen. Für Laurel Brunner, Geschäftsführerin von Digital Dots und Jurymitglied bei den Global Flexo Innovation Awards (GFIA) 2021/2022 ist das keine Überraschung.
„Im heutigen Einzelhandelsumfeld ist die Verpackung so wichtig geworden, weil sie die wesentliche Schnittstelle zwischen einer Marke und ihren Kunden ist“, erläutert sie. „Sie ist das einzige bedeutende Druckerzeugnis, das nicht online repliziert werden kann: Markenartikler und Handel brauchen etwas, um ihr Produkt zu halten und ihre Waren zu liefern. Allerdings sehen sich Markenunternehmen heutzutage vor komplexe Entscheidungen gestellt: Sie müssen zum Beispiel über Nachhaltigkeit und Umweltauswirkungen nachdenken, aber auch die finanzielle Tragfähigkeit und Kostenkontrolle im Auge behalten.“ Nach Auffassung von Laurel Brunner erlebt die Verpackung deshalb eine aufregende neue Innovationswelle.
Flexo-Bedruckstoffe im Wandel
„Auf dem Gebiet der Bedruckstoffe gibt es eine enorme Innovation. Vor allem werden nachhaltigere Materialien entwickelt, die in den entwickelten Märkten von großer Bedeutung sind“, sagt sie. „Allerdings gilt es auch, Faktoren wie Lieferketten, Materialbeschaffung, Effizienz, Lebensmittelsicherheit, Normen und Vorschriften zu berücksichtigen. Einen Bedruckstoff zu finden, der in all diesen Bereichen die gewünschten Eigenschaften und Fähigkeiten bietet, ist wirklich komplex, und es ist faszinierend zu sehen, wie Wissenschaft und Forschung die Dinge vorantreiben.“
Für einige Flexodruckereien und Markenunternehmen hat sich die Suche nach neuen Bedruckstoffen als Teil des Übergangs von Kunststoffen zu Papier manifestiert. Für andere bedeutete dies eine Abkehr von Mehrschicht-Verbundmaterialien (die in der Regel nicht recycelbar sind) und eine Umstellung auf Monomaterial-PE-Substrate (die häufig recycelbar sind).
Biologisch abbaubare Beutel, kompostierbare Tüten, immer dünnere Kunststoffe, leichtere Bedruckstoffe: Die Innovationen kommen schnell und zahlreich. Für Rodney Pennings, Verkaufsdirektor bei PCMC, einem in den USA gegründeten, weltweit aktiven Maschinenhersteller, haben Flexodruckmaschinen in diesem Bereich die Nase vorn. Dank der Fähigkeit dieser Maschinen, ungewöhnliche Bedruckstoffe bei hohen Geschwindigkeiten, in variablen Mengen und mit komplexer Farbflächendeckung zu verarbeiten, konnten seine Kunden Ergebnisse erzielen, die selbst erfahrene Druckveteranen wie ihn immer wieder in Erstaunen versetzen.
„Es gibt Dinge, die wir heute machen, die ich noch vor zwei Jahren nicht für möglich gehalten hätte“, merkt er an. „Doch damit nicht genug – wir machen Dinge, von denen ich nicht einmal gewusst hätte, dass ich danach fragen könnte! Ob nun mit dünneren Bedruckstoffen, PE-Strukturen oder gar Papierbeuteln gearbeitet wird, wir schaffen heute Verpackungslösungen, die noch vor ein oder zwei Jahren nicht möglich gewesen wären.“
Dem Wandel mit neuer Flexotechnologie begegnen
Doch wie immer bringt der Fortschritt auch unweigerlich Herausforderungen mit sich. Rodney Pennings erklärt, dass die Arbeit mit vielen dieser neuen Bedruckstoffe die Druckereien dazu gezwungen hat, sich neue Arbeitsweisen zu eigen zu machen – sei es durch den Einsatz von mehr KI und Automatisierung, um eine Druckmaschine in die Lage zu versetzen, sich automatisch auf eine konsistente Druckausgabe einzustellen, oder durch das Experimentieren mit verschiedenen Druckfarben, Druckplatten und Trocknungsverfahren, um die Farbwiedergabe und den Druckfarbauftrag besser zu regulieren.
Auch wenn die Umstellung nicht immer einfach war, haben Flexodruckmaschinen eine wichtige Rolle dabei gespielt, diesen Wandel zu ermöglichen. Rodney Pennings führt die bessere Deckkraft, den geringeren Druckfarbenverbrauch und die kürzeren Trocknungszeiten – ohne Beeinträchtigung der Druckqualität – als Vorteile des Flexodrucks an, die auch finanziell positiv zu Buche schlagen. „Die Innovationen, welche Miraclon mit seinen KODAK FLEXCEL NX Platten, den FLEXCEL NX Systemen und der Software geschaffen hat, sind einfach unglaublich. Wir sind jetzt in der Lage, bei niedrigeren Temperaturen zu trocknen; wir können eine bessere Opazität bei geringerem Druckfarbenverbrauch erzielen; und, was am wichtigsten ist, wir können dennoch den so wichtigen Aufmerksamkeitseffekt erzielen – die lebendigen Druckbilder und die gleichmäßige Oberflächendeckung, die dazu führen, dass eine Erdbeere immer noch wie eine Erdbeere aussieht, die man tatsächlich essen möchte.“
Resultate liefern
Für Anand Patel, Direktor von Pentaflex, einem auf flexible Verpackungen spezialisierten indischen Unternehmen, ist die Fähigkeit des Flexodrucks, auf ungewöhnlichen Bedruckstoffen hochqualitative Druckresultate zu erzielen, von entscheidender Bedeutung.
Für seine Kunden ist die Recyclingfähigkeit der Verpackungen ein Hauptanliegen: Eine ganze Reihe neuer Industrievorschriften zwingt Markenartikler dazu, von herkömmlichen Kunststoffen auf dünne Polyethylenmaterialien (PE) umzusteigen, die sich leichter recyceln lassen. Bei Anwendungen dieser Art haben Tief- und Offsetdruckmaschinen Schwierigkeiten.
„Für mich kommt der Flexodruck erst richtig zur Geltung, wenn man mit PE arbeitet“, erklärt Anand Patel. „Hier in Indien waren wir mit den richtigen Maschinen zur richtigen Zeit am richtigen Ort, als dieser große Wandel einsetzte.“ Pentaflex stieg vor einigen Jahren mit dem FLEXCEL NX System und Zentralzylinder-Flexodruckmaschinen des Herstellers Bobst in den Flexodruck ein. „Dies eröffnete eine Vielzahl von Möglichkeiten für die Arbeit mit diesen neuen recycelbaren Materialien“, berichtet Anand Patel. „Als Kunden auf uns zukamen und flexobedruckte Polyethylenfolien in einer Qualität auf dem Niveau des Tiefdrucks wünschten, konnten wir ihnen absolut helfen.“
Ob recycelbare Kunststoffe, papierbasierte Produkte, reduzierte Druckfarben oder weniger ressourcenintensive Materialien – mit dem Flexodruck können Verpackungsdruckereien einen großen Schritt in Richtung einer nachhaltigeren Zukunft machen. Laurel Brunner ist gespannt auf das, was die Zukunft bringen wird: „Die Druckindustrie war schon immer eine Branche, die sich den Herausforderungen gestellt und es geschafft hat, sich entsprechend zu verändern und anzupassen. Doch die eigentliche Innovation vollzieht sich im wissenschaftlichen Bereich. Stellen wir uns eine Verpackung vor, die auf weißem Papier phänomenal aussieht, aber dann soll Karton verwendet werden. Wie schafft man es, dass das Drucksujet auf beiden Materialien gleich herauskommt? Das ist eine Frage der Wissenschaft. Und meiner Meinung nach findet gegenwärtig die interessanteste wissenschaftliche Entwicklung in der Welt der Substrate statt. Ich kann es wirklich kaum erwarten, zu sehen, was als Nächstes kommt.“